Essential Guide: 10 Key Features to Evaluate When Choosing an Industrial CNC Machine
In today's fast-evolving manufacturing landscape, selecting the right Industrial CNC Machine is crucial for optimizing production efficiency and maintaining competitive advantage. With various models and capabilities available, it is essential for manufacturers to navigate through the myriad of options to identify a machine that aligns with their specific needs and production goals. This essential guide aims to shed light on the ten key features that should be evaluated during the selection process of an Industrial CNC Machine. From precision and speed to ease of use and software compatibility, understanding these fundamental attributes will empower manufacturers to make informed decisions, ensuring they invest in a machine that not only meets their current demands but also prepares them for future growth and technological advancements in the industry.
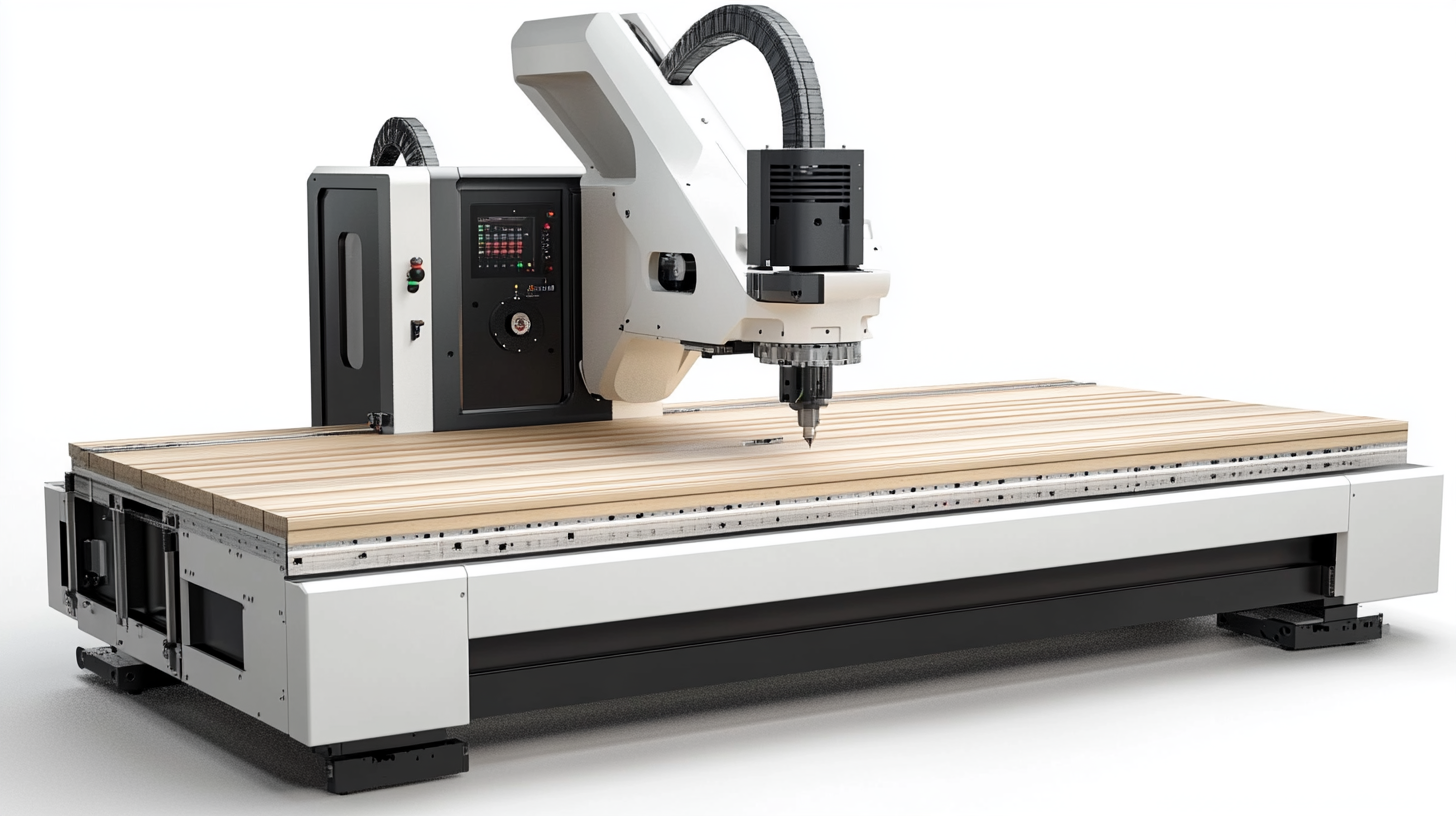
Understanding the Importance of Precision in CNC Machines
When selecting an industrial CNC machine, one cannot underestimate the significance of precision. According to a report by MarketsandMarkets, the global CNC machine market is projected to reach $100 billion by 2025, driven primarily by the increasing demand for high precision and accuracy in manufacturing processes. Precision CNC machines enable manufacturers to produce intricate components with tolerances as tight as ±0.005 mm, which is crucial for industries where even the slightest deviation can lead to costly errors or safety hazards.
The importance of precision is further highlighted by a survey conducted by Deloitte, which revealed that 72% of manufacturers believe that precision machining is essential for digital transformation and innovation. As industries embrace technologies like Industry 4.0, the role of precision increases, allowing for enhanced automation and seamless integration of processes. High-precision CNC machines not only minimize material waste, but they also improve overall production efficiency and product consistency. Investing in machinery capable of delivering exceptional precision is, therefore, not just a cost—it's a strategic move for businesses aiming to stay competitive in a rapidly evolving marketplace.
Key Features to Evaluate When Choosing an Industrial CNC Machine
This pie chart illustrates the importance of various features when selecting an industrial CNC machine, highlighting precision, speed, versatility, and other key considerations for effective machining.
Assessing the Material Compatibility for Your CNC Projects
When choosing an industrial CNC machine, one of the most crucial aspects to consider is the material compatibility for your specific projects. Different CNC machines are designed to work with various materials, ranging from metals and plastics to wood and composites. Understanding the material properties and requirements is essential to ensure that the machine you invest in can handle the necessary processes, whether milling, turning, or routing.
When assessing material compatibility, focus on the machine's capabilities regarding hardness, thickness, and elasticity of the materials in question. For instance, if your projects involve machining hard metals, such as titanium or hardened steel, you’ll need a CNC machine equipped with a powerful spindle and robust tooling that can withstand the demanding nature of these materials. Conversely, if your focus is on softer materials like foam or plastic, a less powerful machine may suffice, allowing for more flexibility and cost-effectiveness in your choice.
Additionally, consider the machining techniques required for your materials. Some materials may necessitate special tooling or coolant systems to maintain temperature control and surface finish during machining. Therefore, it’s vital to match your machine's features with the specific requirements of the materials you intend to work with, ensuring optimized performance and quality results in your CNC projects.
Essential Guide: 10 Key Features to Evaluate When Choosing an Industrial CNC Machine
Feature | Description | Importance | Material Compatibility |
---|---|---|---|
Spindle Power | Refers to the motor power that drives the spindle, affecting cutting efficiency. | High | Metals, Composites |
Axis Configuration | The number of axes available for movement, impacting the complexity of operations. | Medium | Plastics, Wood, Metals |
Cutting Speed | The speed at which the CNC machine can cut through materials. | High | All Materials |
Tooling Options | Variety of tools available for different machining operations. | High | Metals, Composites, Plastics |
Software Compatibility | Ease of use and integration with CAM software. | Medium | All Materials |
Precision and Accuracy | The capability to produce parts with tight tolerances. | High | Metals, Composites |
Workpiece Size | Maximum dimensions of the materials that can be machined. | Medium | Large Materials |
Cooling System | Type of cooling mechanism to maintain tool performance. | High | Metals |
Maintenance Requirements | Frequency and type of maintenance needed for the CNC machine. | Medium | All Materials |
Initial Cost vs. ROI | Analysis of the investment cost compared to anticipated returns. | High | All Materials |
Evaluating Software Compatibility and User Interface Experience
When choosing an industrial CNC machine, the importance of evaluating software compatibility and user interface experience cannot be overstated. A CNC machine is only as efficient as the software that drives it, making compatibility with design programs and other tools vital for a seamless workflow. Investigate whether the CNC machine supports popular software such as CAD/CAM, as this can significantly affect production quality and speed. Additionally, check the availability of software updates or plugins that enhance functionality, which can help keep your operations at the forefront of technology.
User interface experience is equally crucial in selecting the right CNC machine. An intuitive interface can greatly reduce the learning curve for operators, leading to increased productivity and fewer errors. Look for machines that offer touchscreen controls, customizable dashboards, and clear navigation systems. These features streamline the setup and operation processes, allowing users to focus more on their tasks rather than struggling with complicated menus. A positive user interface experience not only fosters confidence among operators but also minimizes downtime, paving the way for more efficient production practices in your industrial operations.
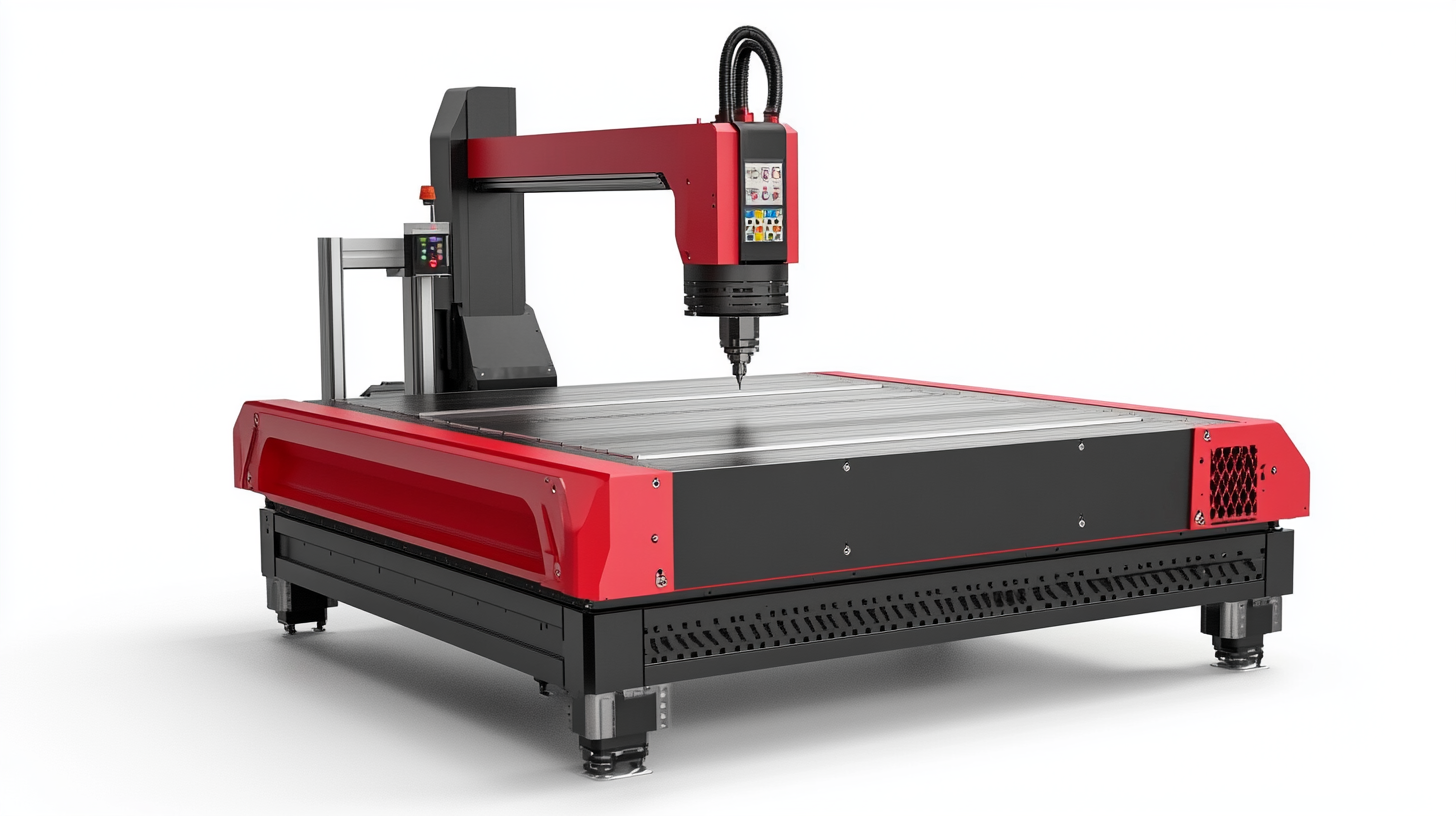
Examining Machine Size and Workspace Requirements
When evaluating an industrial CNC machine, one critical aspect to consider is the machine size and workspace requirements. The dimensions of the CNC machine must align with the operational space available in the manufacturing facility, ensuring that there is sufficient room for both the machine and any necessary tools or materials. A compact design might be preferable for smaller workshops, while larger operations may benefit from machines with more extensive workspaces that allow for bigger projects or simultaneous machining of multiple components.
Recent advancements in robotic technology, such as the development of versatile mechanical grippers, illustrate the trend towards machines that can perform tasks akin to human dexterity. This flexibility is essential not just in automation but also in CNC machining, where precise handling of materials can influence production efficiency. As industries seek to maximize their capabilities, understanding how a machine's workspace can accommodate different operations will be key to optimizing workflow and achieving high-quality outcomes.
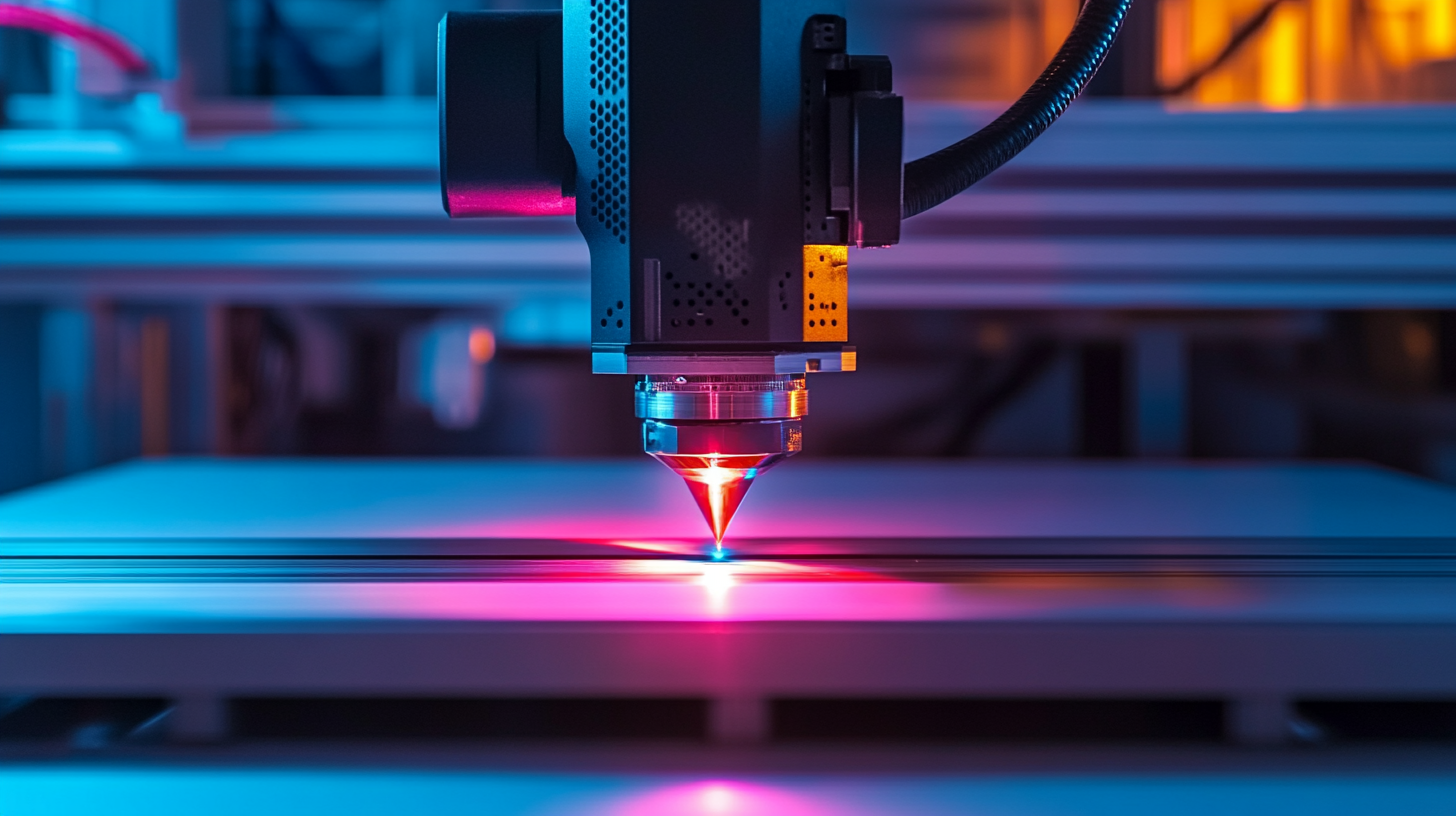
Exploring Maintenance Needs and Support Options for CNC Machines
When selecting an industrial CNC machine, one of the most critical aspects to consider is the maintenance needs and support options available. Regular maintenance is crucial for ensuring optimal performance and extending the lifespan of CNC machines. According to a recent report by MarketsandMarkets, the global CNC machine market is expected to grow at a CAGR of 5.2% from 2020 to 2025, indicating that companies are increasingly relying on these technologies. However, without proper maintenance, machines can suffer from downtimes that negatively impact production efficiency.
Moreover, support options should also be a priority in your evaluation. Many manufacturers offer varying levels of after-sales support, from remote troubleshooting to on-site service, which can significantly reduce downtime. A survey by the Association for Manufacturing Technology (AMT) indicated that businesses with robust maintenance support reported a 20% reduction in unplanned machine outages. Investing in CNC machines that come with comprehensive support packages can yield long-term cost savings and enhance productivity, making it essential to assess these features when making your choice.