Transforming Manufacturing: 2025 Innovations in CNC Turning Machines & Buyer’s Guide
The very nature of manufacturing is undergoing unprecedented changes as we move into the 2025 horizon. Technological advancement is indeed a great fulcrum in this entire scenario. The CNC turning machine is probably one of the most important innovations in this transformation, making it an entire discipline in precision engineering. These machines do not only do the job of increasing productivity, but they also allow for manufacturing operations that are otherwise done in incomparable accuracy and efficiency. Therefore, it becomes quintessential for industries to familiarize themselves with these latest trends and technologies so they can make wise buying decisions in CNC turning machines.
The blog will introduce the innovations in CNC turning machines, which are to be expected by 2025, and will present an exhaustive buyer's guide to help one sort through these emerging technologies. From smart automation features to advanced material capabilities, innovation in the coming era is sure to redefine the way manufacturers do their job. Whether you're weighing your options as an informed buyer or are stepping into the domain of CNC machinery for the first time, the insights here will arm you with the knowledge necessary for making choices that support your production objectives. Let us embark on examining the future of manufacturing through the vantage of CNC turning technology.
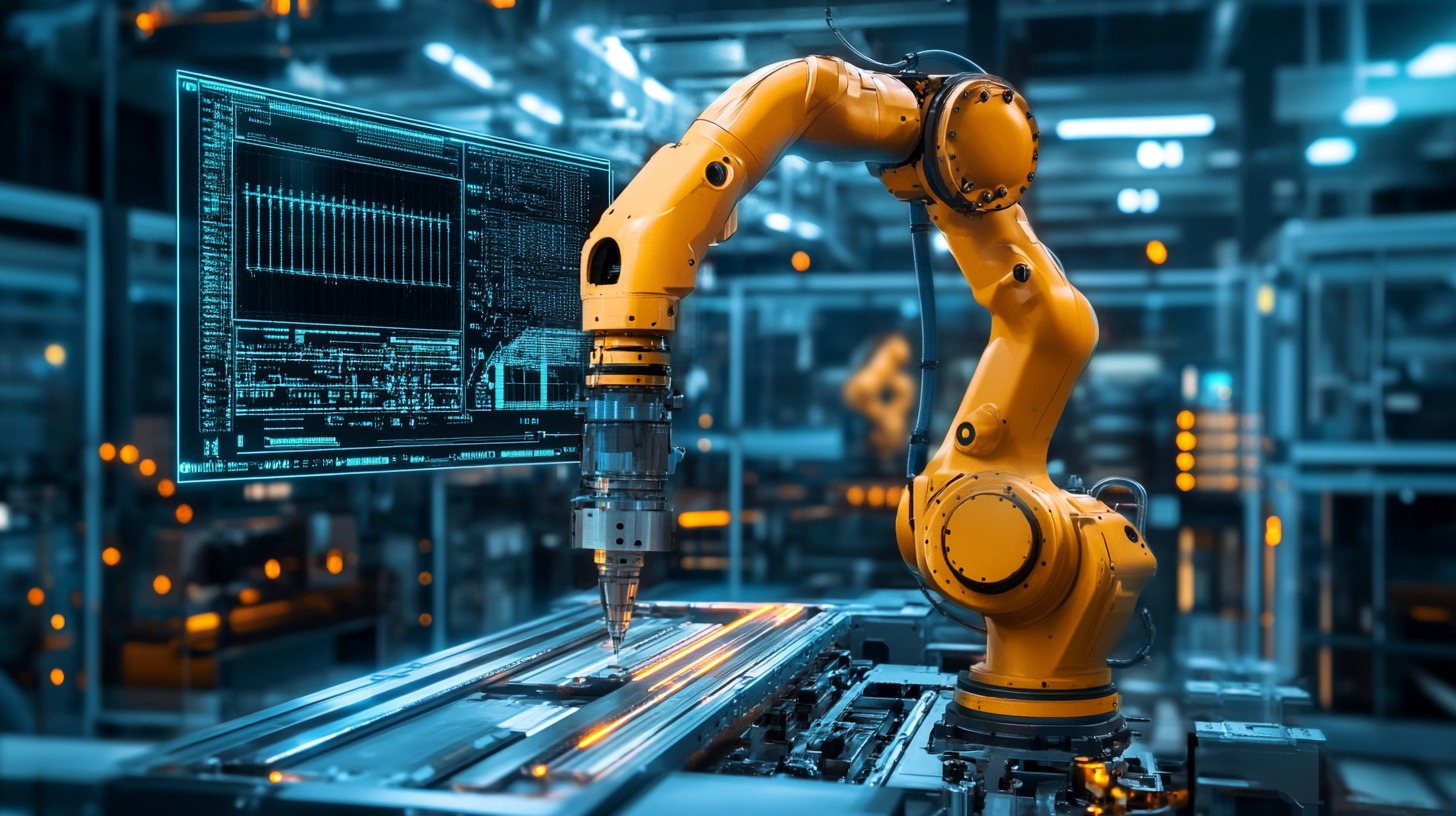
The Future of CNC Turning Machines: Key Trends Shaping the Industry by 2025
The CNC turning machine industry appears on the verge of significant changes as we near the year 2025. Various trends are emerging, which will ultimately become the backbone of a changing horizon dictated by technology and smart manufacturing. Man and machine concepts employing intelligent manufacturing processes have gained priority, with companies investing heavily in automation and data-enabled solutions. This paradigm not only enhances production efficiency but also contributes towards precision and quality in machining. Governments worldwide are preparing for the upcoming transformation. Policies relating to the modernization of manufacturing technologies are being adopted and are now supporting the establishment of advanced manufacturing clusters. This is highly apparent in those regions recognized as key players in the CNC machine tool sector: local governments will roll out incentives for production and innovation. Further, high-end CNC machines are gaining importance. Manufacturers are increasingly changing towards these advanced solutions that offer improved capabilities for complex machining tasks. As new players enter this sector and the market becomes increasingly competitive, the CNC turning machines' landscape is changing at a rapid pace, for the setting up of a future denoting innovation and industrial capabilities.
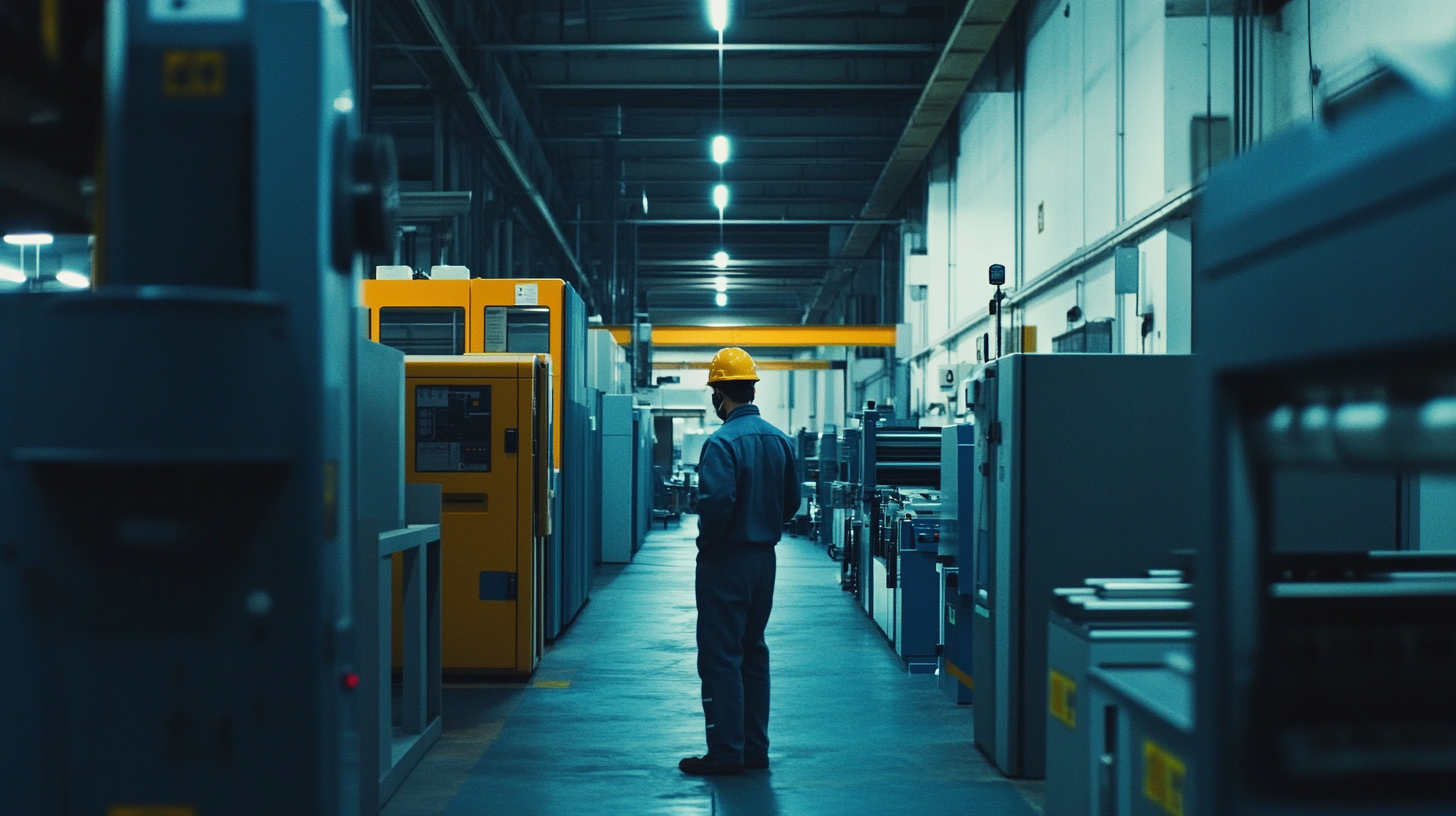
Understanding the Impact of Industry 4.0 on CNC Turning Technology
By the lens of Industry 4.0, manufacturing transformation is bringing about wondrous changes in CNC turning technology. As we move toward 2025, the combination of automation and intelligence in CNC machining surroundings is expected to radically change efficiency and precision. The very new developments make machines not just capable of operating autonomously, but also able to talk to one another and thus form smarter production lines that can dynamically change with fluctuations in demand or operating conditions.
In this transitory state, models such as those in Virginia Tech and Kogakuin University operate with students on the premises of learning by doing Industry 4.0. These initiatives are instrumental in preparing a new generation of youngsters who will thrive in the world of heavy automation. The important factor that will be emphasized concerning smart factory notions is the interdisciplinarity required from engineering to computer science so that graduates are able to face whatever may come in the future concerning manufacturing.
Additionally, from more recent market analysis, the CNC machine scene is said to grow significantly, driven by advances in both metal cutting and forming technologies. As industries shift towards incorporating these innovative machines, the demand for precision and efficiency will thus commence meaning that an elaborate buyer's guide has to feature key points and functionalities needed in today's manufacturing environment. This ever-evolving nature verifies the fact that Industry 4.0 is not just a word deemed applicable-anymore-but practically a game changer of CNC turning technology.
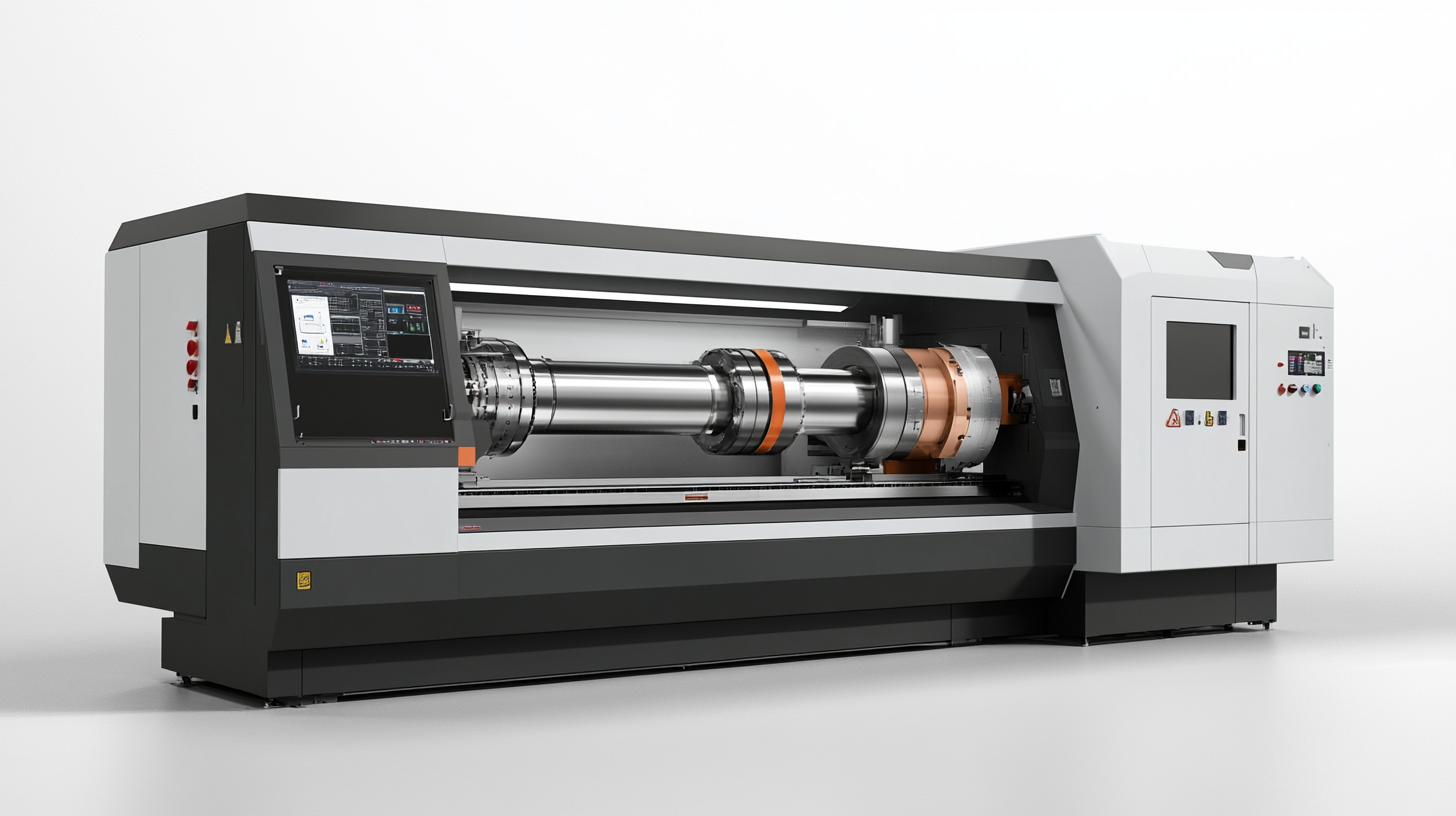
Data-Driven Insights: The Role of Big Data in Optimizing CNC Operations
The integration of big data into CNC operations provides a new perspective to manufacturing under Industry 4.0. CNC turning machines are fitted with sensors and data analytics, allowing manufacturers to gather and analyze huge amounts of operational data in real-time. This operational data proves essential in determining inefficiencies, predicting maintenance requirements, and optimizing production processes. Companies can then utilize big data to improve precision and lessen wastes for profit maximization.
Though big data may create greater efficiencies, it offers manufacturers the ability to make decisions based on knowledge accumulated through thorough analysis instead of mere intuition. The implications of predictive analytics embrace not only foreseeing possible situations but also preemptive maintenance of CNC turning machines to limit the time of tools sitting idle. Training with machine-learning algorithms also allows CNC turning machines to fine-tune their functions against the operational space with the constant adjustment of changing demands. This fine-tuning guarantees smarter productivity while increasing product output quality.
Big data also contributes to more integrated supply chain management. With such trend analysis, manufacturers can manage inventory levels, perform maintenance before the onset of malfunctions, and align their production scheduling with demand in the marketplace. With that in mind, manufacturing processes can be much more resilient to market fluctuations while being streamlined with the aid of this data aggregation or data management model. As CNC technology develops, this interrelationship between big data and machining will remain a critical cog for businesses willing to prosper in a competitive scene.
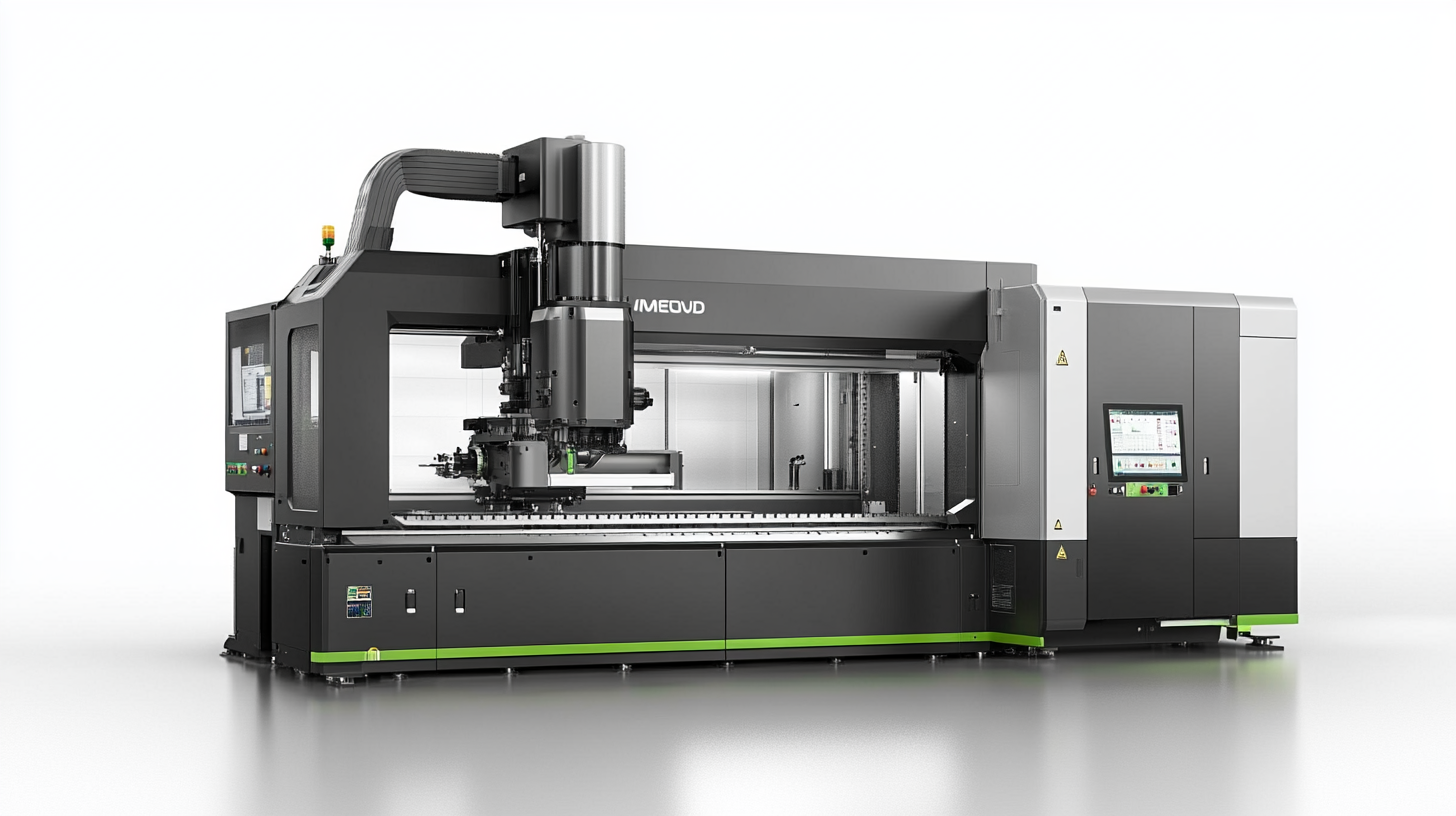
Essential Features to Look for in Modern CNC Turning Machines
CNC turning machines in manufacturing have become real vectors of precision and efficiency over the years. In the near future, by 2025, production will be transformed by the different innovations this technology promises. Therefore, before embarking on purchasing a new CNC turning machine, prospective buyers must understand the essential features for consideration with modern CNC turning machines.
Modern machines have key functionalities such as advanced software integration capable of real-time monitoring and control. This means that almost all activities can be done in optimizing performance and reducing down-times. Multi-axis capabilities are further added features that boost flexibility in terms of what geometry can be machined and what a machine can run. Other features that are most likely going to entice prospective buyers are improved automation and robotics integration-an aspect that streamlines operations but also takes safety measures on the factory floor.
In addition, it is becoming relevant and most important that a machine is IoT-ready, which can collect and analyze the data smoothly so that performance can be measured and smart decisions can be made by the manufacturers. As intelligent manufacturing becomes a trend, buying a CNC turning machine rich in modern technology's best will have a strong impact on the industry's competitive edge and will capitalize on innovation in the manufacturing sector today.
Navigating the Market: A Comprehensive Buyer’s Guide for CNC Equipment in 2025
In 2025, there are going to be drastic changes in the manufacturing domain. One of the areas where there are going to be very high effects in terms of change is CNC turning machines. With increasing industry adoption of both automation and precision engineering, the market for CNC machine tools is going to reach a state of hyped growth. This is because it keeps getting improved through technological wonders that underpin efficiency and reduce wastes while at the same time improving product quality, thereby making CNC machines very essential investments for manufacturers involved in various activities such as automotive, general machinery, and precision engineering.
To be competitive in the CNC machinery business in 2025, it is quite simple to say that one has to be very well informed about the offerings within that space. Parameters should be noted – capabilities of machines, compatibility to existing manufacturing system, and specific applications for which the business wants. Also, having entered the fray alongside evolving indigenous companies within the industrial automation sector, manufacturers have more options that promise to offer quality comparable to that of international players at friendly prices. Market trends including geographical differences are important for buyers to recognize to make intelligence out of scouting into strategic decisions.
This segment further underscores the importance of metal cutting and forming, as indeed, these are the processes in which CNC shines. Industries also derive specific benefits from custom-tailoring solutions to specific production concerns. Companies such as those found in Dongguan, which adopt CNC machining, are a living test case in how innovation and a focus on quality lead to sustained competitive advantage in a crowded marketplace today.