Unlocking Efficiency in Global Procurement: Mastering CNC Turning Techniques for Optimal Sourcing
The landscape of global procurement is rapidly evolving, with companies increasingly seeking ways to streamline their supply chains and enhance operational efficiency. A key factor in achieving these objectives is the adoption of advanced manufacturing techniques, particularly CNC turning. According to a report by MarketsandMarkets, the CNC machining market is projected to reach USD 100.3 billion by 2026, with a significant portion driven by the rising demand for precision-engineered components across various industries such as automotive, aerospace, and electronics. This growth highlights the importance of mastering CNC turning techniques, which can significantly improve sourcing strategies and reduce costs while maintaining high-quality standards.
CNC turning offers a level of automation and precision that traditional machining processes often struggle to achieve. A study published by Grand View Research noted that automation in manufacturing processes, including CNC turning, could enhance productivity by as much as 20%. By integrating these advanced techniques into their procurement strategies, organizations can not only optimize their sourcing efforts but also respond more swiftly to market changes and customer demands. In this blog, we will explore how mastering CNC turning techniques can unlock efficiency in global procurement, providing actionable insights on implementation and best practices that will set you ahead in today’s competitive landscape.
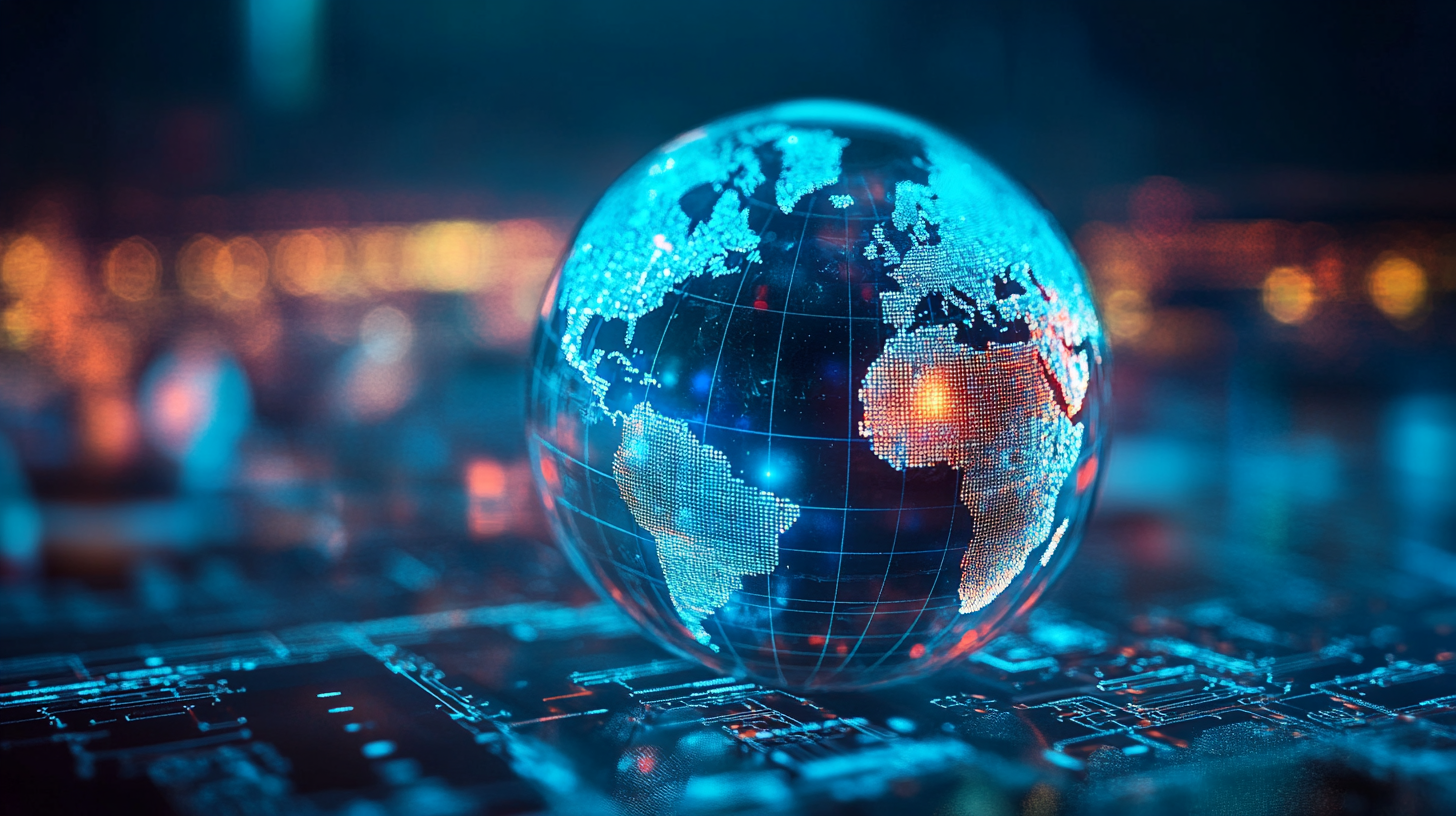
Understanding CNC Turning: A Key Component in Global Procurement Strategies
CNC turning techniques play a pivotal role in global procurement strategies by enhancing efficiency and precision in the manufacturing process. At its core, CNC (Computer Numerical Control) turning involves the use of automated machinery to produce highly accurate cylindrical components. This technology not only reduces human error but also accelerates production timelines, allowing organizations to meet global demand swiftly. As businesses aim to streamline their operations, understanding CNC turning becomes essential for optimizing sourcing decisions and managing supply chains effectively. Integrating CNC turning into procurement strategies offers a multitude of benefits. First, it allows for the production of complex geometries that are often required in modern manufacturing. This versatility enables companies to source components without being limited to conventional machining processes. Moreover, CNC turning ensures consistent quality across batches, which is crucial for maintaining standards in global markets. Leveraging this technology can lead to better supplier partnerships, as companies that understand and utilize CNC capabilities are more likely to succeed in negotiating favorable contracts and managing inventory effectively. As global competition intensifies, mastering CNC turning techniques not only enhances product quality but also influences cost efficiencies. Companies investing in advanced CNC machinery can reduce waste, minimize turnaround times, and lower operational costs, fostering a more agile procurement strategy. In the ever-evolving landscape of global manufacturing, understanding and implementing CNC turning techniques is imperative for businesses aiming to stay ahead in their procurement efforts.
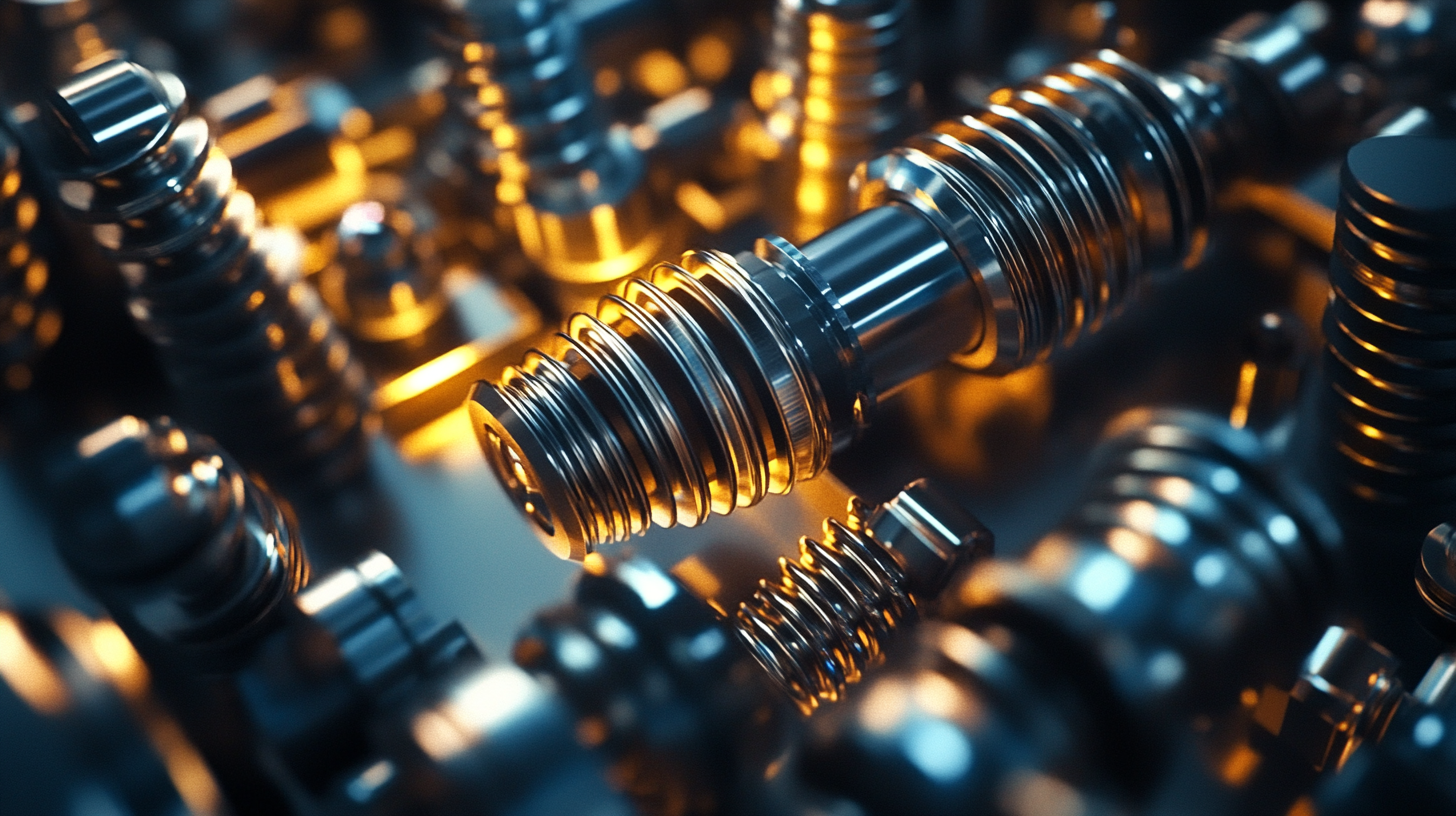
Innovative Techniques for Enhancing CNC Turning Efficiency
In the fast-paced world of global procurement, enhancing efficiency through innovative CNC turning techniques is essential for businesses seeking to optimize their sourcing strategies. CNC turning has evolved significantly, integrating advanced technologies that allow for greater precision and reduced cycle times. By leveraging these innovations, companies can streamline their production processes, leading to reduced costs and improved product quality.
One of the most impactful techniques in modern CNC turning is the utilization of adaptive control systems. These systems allow machines to adjust their operations in real-time, responding to variations in materials and tooling conditions. By implementing adaptive control, manufacturers can minimize downtime and maintain consistent quality, ensuring that production schedules are met without compromising on performance. Additionally, incorporating machine learning algorithms can enhance the predictive capabilities of CNC turning equipment, enabling operations to foresee potential issues before they arise.
Another innovative approach involves the integration of advanced cutting tools and materials. The development of high-performance cutting inserts and coatings has dramatically improved the life and efficiency of tools used in CNC turning. By selecting the right tooling for specific materials and applications, manufacturers can increase cutting speeds and feed rates, leading to shorter machining times and decreased operational costs. Furthermore, these advancements contribute to improved surface finishes and dimensional accuracy, which are crucial in meeting the demands of today’s competitive market.
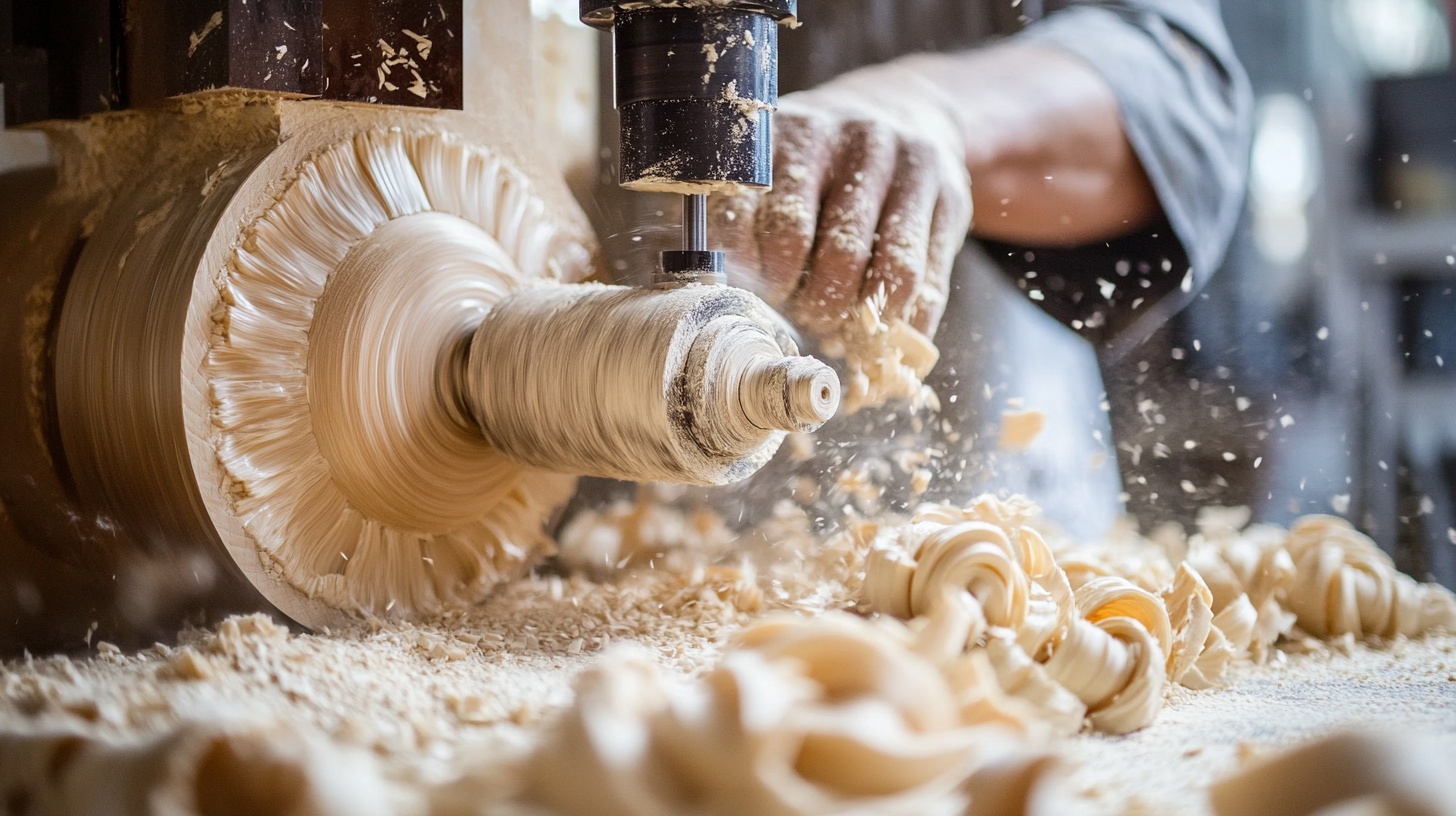
Evaluating Supplier Performance: Metrics for Effective Procurement
In the realm of global procurement, supplier performance evaluation has emerged as a critical factor that directly impacts efficiency and cost-effectiveness. As industries increasingly rely on precision manufacturing techniques like CNC turning, understanding key performance metrics is essential for optimizing sourcing decisions. According to a report by McKinsey & Company, organizations that rigorously assess supplier performance improve their procurement outcomes by up to 20%, showcasing the tangible benefits of a systematic approach.
Key metrics for effective procurement include on-time delivery rates, quality assurance scores, and cost competitiveness. A recent survey by Deloitte indicates that 70% of procurement professionals prioritize these metrics, with quality being identified as the most significant factor influencing supplier selection. This focus not only aids in establishing a reliable supplier base but also enhances collaboration between procurement teams and suppliers, driving continuous improvement in processes.
Moreover, implementing technology-driven solutions, such as supplier performance dashboards, can further refine evaluation processes. A study from Gartner highlights that organizations utilizing performance analytics experience a 15% increase in supplier efficiency. By leveraging such tools, procurement professionals can gain actionable insights that inform strategic sourcing decisions, ultimately leading to more sustainable and profitable procurement practices in the competitive landscape of CNC turned components.
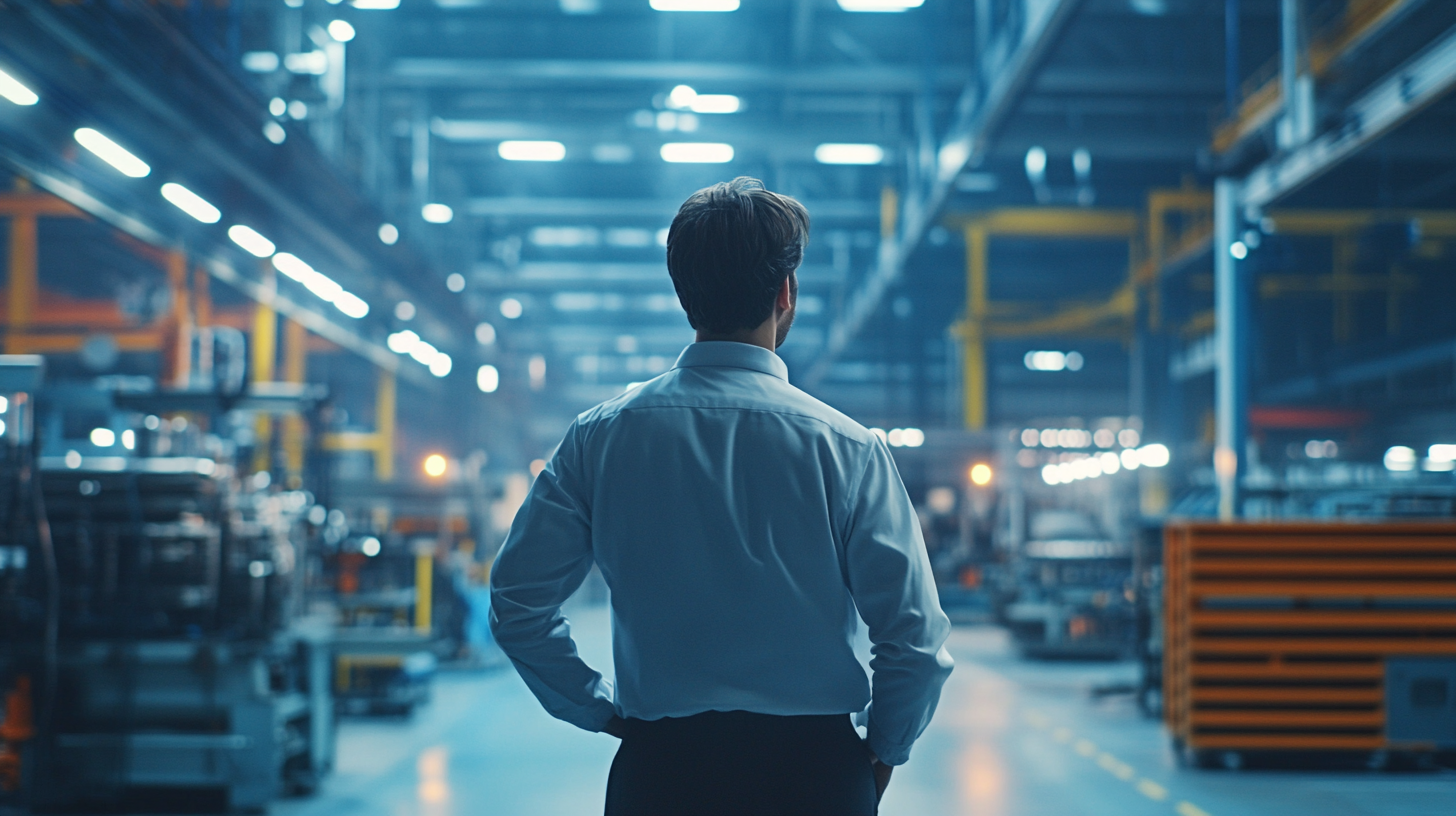
Cost Reduction Strategies through Advanced CNC Turning Practices
In the realm of global procurement, cost efficiency is paramount. One effective way to achieve significant savings is through advanced CNC (Computer Numerical Control) turning techniques. By mastering these techniques, businesses can streamline their sourcing processes, reduce waste, and ultimately lower production costs. The precision and automation of CNC machines not only enhance the quality of the finished products but also minimize the time and labor required for manufacturing.
Implementing advanced CNC turning practices allows companies to optimize their supply chain. For instance, utilizing high-speed machining capabilities can reduce cycle times, allowing for quicker turnaround on orders. Moreover, employing state-of-the-art materials and cutting tools can decrease the frequency of tool changes and maintenance, leading to less downtime and increased productivity. These improvements do not just contribute to immediate cost reductions but also foster a reliable production schedule, which is essential in competitive markets.
Additionally, leveraging predictive analytics and machine learning technologies within CNC turning operations can provide valuable insights into operational efficiencies. By analyzing data patterns related to production processes, companies can identify areas of overspending and adjust their strategies accordingly. This data-driven approach leads to more informed decision-making in procurement, ensuring that businesses are not only sourcing components at the best prices but also optimizing the entire manufacturing workflow for better overall cost efficiencies.
Integrating Technology: The Future of CNC Turning in Global Sourcing
As businesses continue to navigate the complexities of global procurement, integrating advanced technology into CNC turning processes has emerged as a critical strategy for enhancing efficiency and accuracy. The advent of Industry 4.0 has paved the way for smart manufacturing techniques that harness the power of connectivity and data analytics, allowing organizations to optimize their sourcing efforts. Through real-time monitoring and predictive maintenance, businesses can minimize downtime and streamline operations, ensuring that their CNC turning capabilities remain competitive in a fast-paced market.
The future of CNC turning in global sourcing is characterized by the adoption of automation and artificial intelligence. By leveraging these technologies, manufacturers can achieve higher precision and reduce lead times. Automated CNC machines equipped with intelligent software can adapt to varying production demands, making it easier to manage complex supply chains. Moreover, the integration of cloud computing enables seamless data sharing among suppliers and manufacturers, fostering collaboration and enhancing decision-making processes.
As the landscape of global procurement evolves, CNC turning techniques will play a pivotal role in achieving optimal sourcing outcomes. Companies that invest in these technologies are not only boosting their operational efficiency but also positioning themselves to respond rapidly to market changes. By embracing innovation in CNC turning, organizations can unlock new levels of efficiency, reduce costs, and enhance product quality, ensuring sustainability in their global sourcing strategies.