Exploring Cnc Machine Technologies Shaping the Future of Global Manufacturing by 2025
In the rapidly evolving landscape of global manufacturing, the advent of CNC (Computer Numerical Control) machine technologies stands out as a transformative force. By 2025, these innovations are expected to redefine not just how products are manufactured, but also the very nature of industrial operations. At the heart of this revolution is the concept of CNC machine working, a process that enables unparalleled precision and efficiency, allowing manufacturers to meet the growing demands of customizability and complexity in their production lines. As industries increasingly adopt these advanced methodologies, understanding their implications becomes crucial for stakeholders at every level.
This blog delves into the key technologies within CNC machine working that are steering the future of manufacturing. From the emergence of intelligent automation to the integration of additive manufacturing techniques, we will explore how these advancements are not only enhancing operational capabilities but also driving sustainability and innovation. As we navigate through the intricacies of CNC machine technologies, it becomes clear that their influence will extend far beyond traditional manufacturing, reshaping the global economy and transforming the workforce of tomorrow.
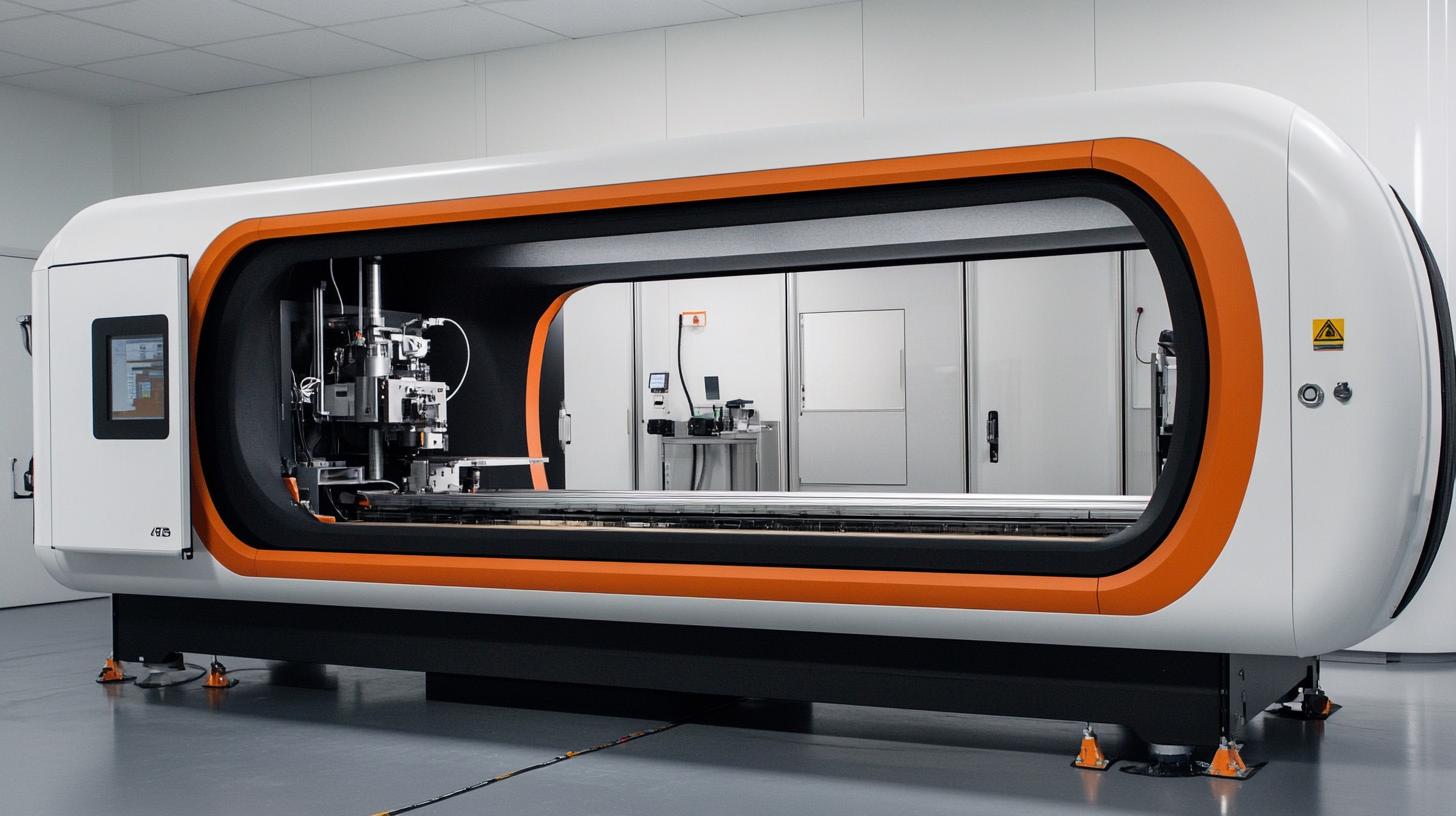
The Evolution of CNC Technologies: A Historical Perspective
The evolution of CNC (Computer Numerical Control) technologies has dramatically transformed the landscape of manufacturing since its inception in the mid-20th century. Originally developed in the 1940s and 1950s, CNC technology replaced manual machines, allowing for greater precision, efficiency, and repeatability. Early systems relied on punched tape for programming; however, advancements in computer technology soon enabled more sophisticated programming languages and interfaces that streamlined the manufacturing process. The introduction of CAD (Computer-Aided Design) software played a pivotal role, allowing designers to create intricate models that machines could interpret with unparalleled accuracy. As we moved into the late 20th and early 21st centuries, CNC technology continued to advance, incorporating features such as multi-axis machining and automation. These enhancements not only improved the capability of CNC machines but also facilitated the rise of complex manufacturing processes, including additive manufacturing and hybrid systems that combine subtractive and additive methods. The result has been an increase in production capabilities, enabling manufacturers to produce highly intricate components and reducing production times significantly. Today, we stand on the cusp of a new era in CNC technology, influenced heavily by emerging trends such as Industry 4.0, where connectivity and collaboration integrate seamlessly into manufacturing ecosystems. With machine learning and artificial intelligence, CNC machines are becoming smarter, predicting failures and optimizing operations. This ongoing evolution presents exciting possibilities for the future of global manufacturing, where precision, efficiency, and innovation will be paramount as we approach 2025 and beyond.
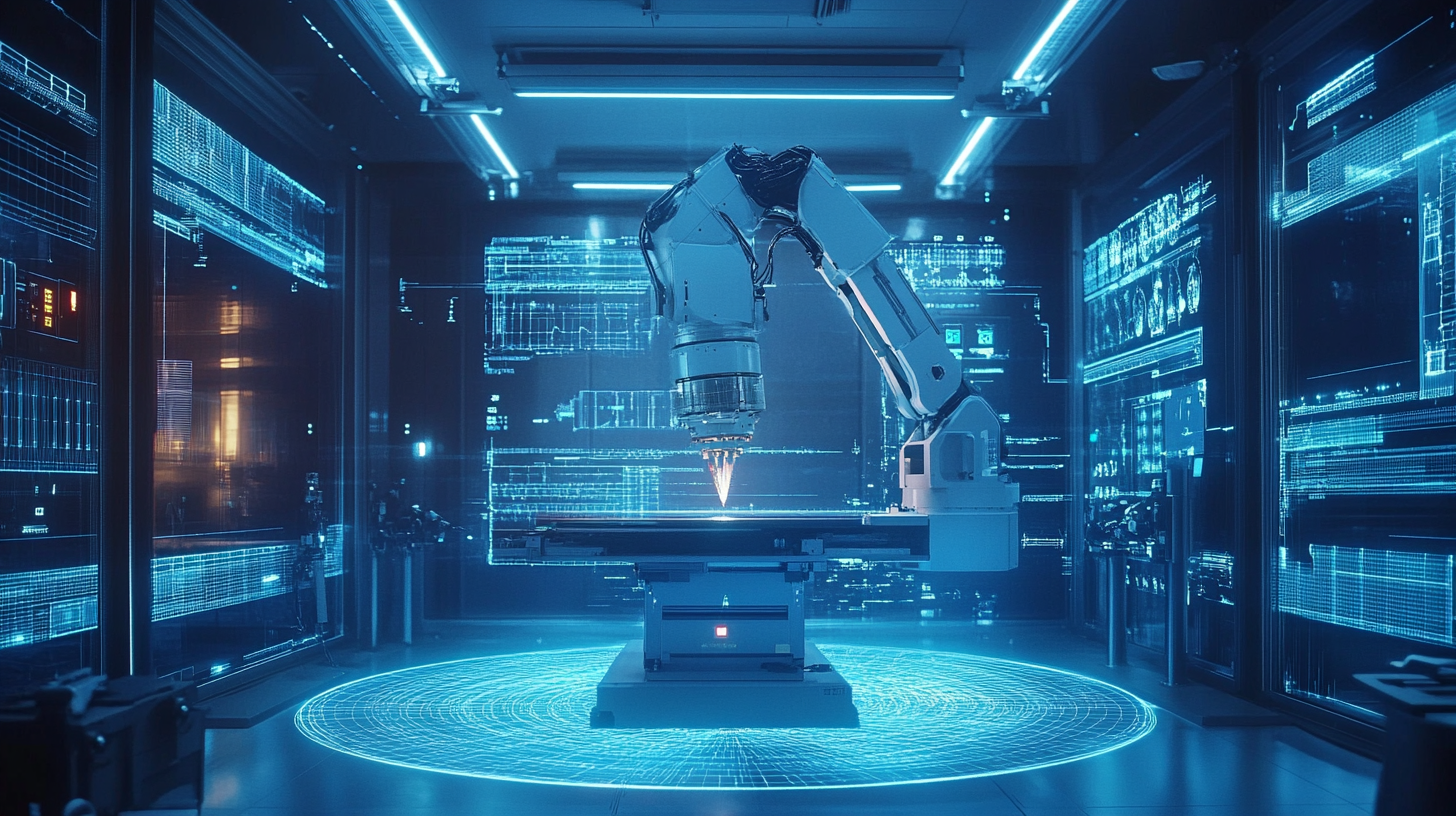
Key CNC Machine Innovations Driving Industrial Efficiency
As we delve into the transformative world of CNC machine technologies, it's evident that several key innovations are poised to drive industrial efficiency by 2025. The global CNC machining market, valued at approximately $63 billion in 2020, is projected to expand at a CAGR of around 6% over the next few years, significantly impacting manufacturing processes across various sectors. This growth is primarily fueled by advancements in automation, precision, and speed of CNC machinery.
One of the most notable innovations is the integration of artificial intelligence (AI) and machine learning into CNC systems. According to a recent report by MarketsandMarkets, the AI in manufacturing market is expected to reach $16.7 billion by 2026, up from $1.5 billion in 2020, indicating a growing trend towards smarter, more efficient workflows. AI-enhanced CNC machines can predict maintenance needs, optimize production schedules, and reduce downtime, ultimately leading to increased productivity and cost savings for manufacturers.
Additionally, the rise of Internet of Things (IoT) technology is revolutionizing CNC operations. IoT-enabled CNC machines can communicate with each other and with central data systems, providing real-time insights into machine performance and production metrics. A study from Deloitte highlights that implementing IoT solutions in manufacturing can improve operational efficiency by up to 30%. This connectivity allows for better resource management, timely maintenance, and a more agile response to market demands.
As the manufacturing landscape continues to evolve, the advancements in CNC technologies—particularly those driven by AI and IoT—will undoubtedly play a pivotal role in shaping the future of global manufacturing, enhancing not only efficiency but also competitiveness in a rapidly changing marketplace.
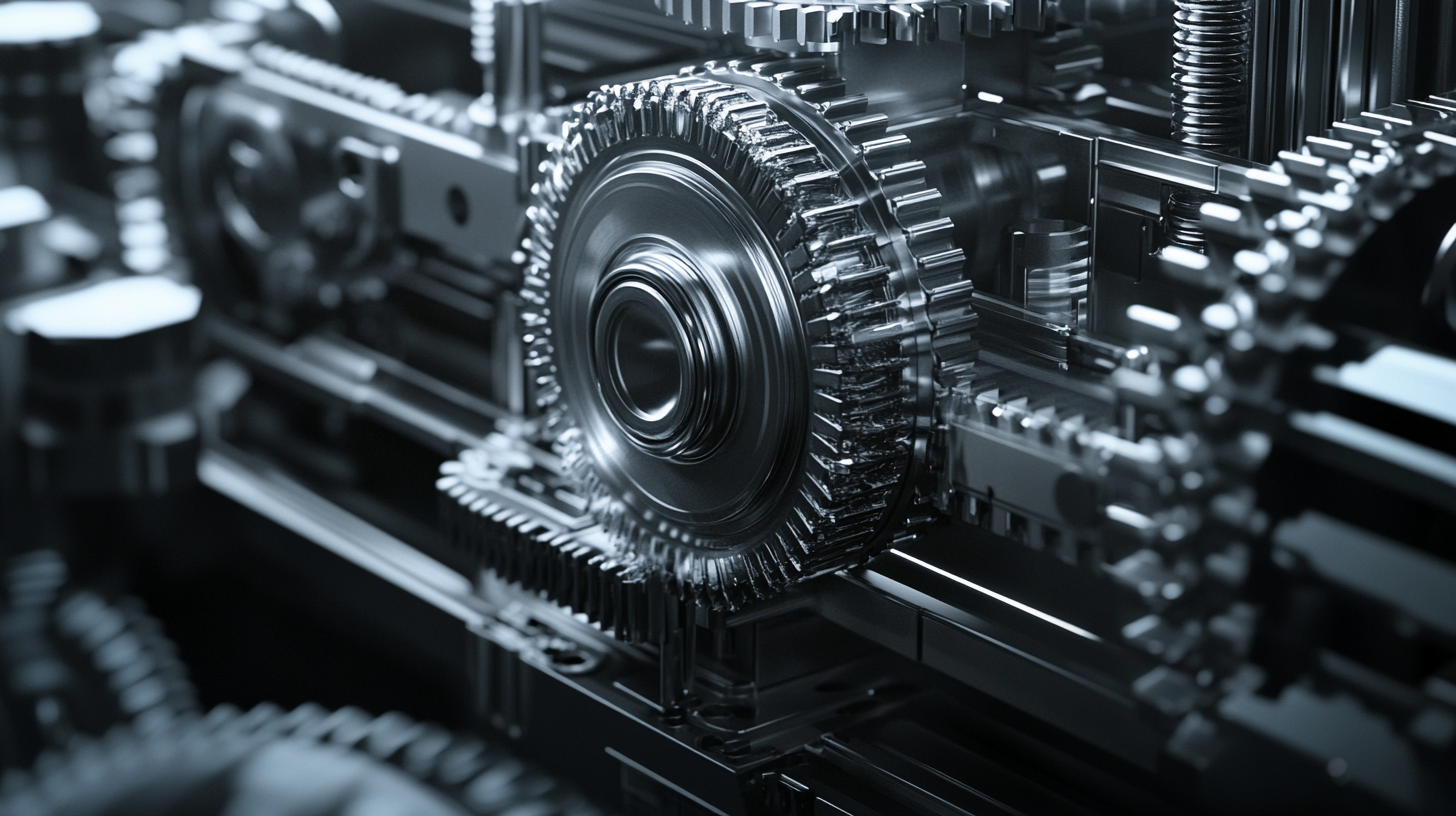
Impact of CNC Machine Technologies on Product Customization
The impact of CNC machine technologies on product customization is becoming increasingly significant as manufacturers strive to meet the diverse demands of global markets. By 2025, the CNC machining market is expected to see substantial growth, buoyed by advancements in automation and IoT. According to industry reports, the global CNC machine tool market size was valued at approximately $80 billion in 2022 and is projected to reach around $120 billion by 2025, highlighting a compound annual growth rate (CAGR) of over 10%.
One of the prominent features of CNC technology is its ability to enhance product customization across various sectors. This capability is particularly crucial in industries such as automotive and aerospace, where tailored solutions are often necessary. As manufacturers increasingly adopt CNC machinery, they can produce complex geometries and personalized designs at scale, thereby responding more accurately to market demands. Research indicates that CNC machining offers up to 50% faster turnaround times for custom parts compared to traditional manufacturing methods, making it an essential tool for competitive businesses.
Moreover, the segmentation of CNC machines by application reveals a rising trend in precision mechanics and transport equipment, expected to dominate the market share. These segments not only underscore the versatility of CNC technologies but also emphasize their pivotal role in precision manufacturing. By leveraging advanced CNC capabilities, companies can achieve tighter tolerances and superior finishes, paving the way for innovation in product development. This transition towards customized production models, driven by CNC technology, is set to redefine the future landscape of global manufacturing.
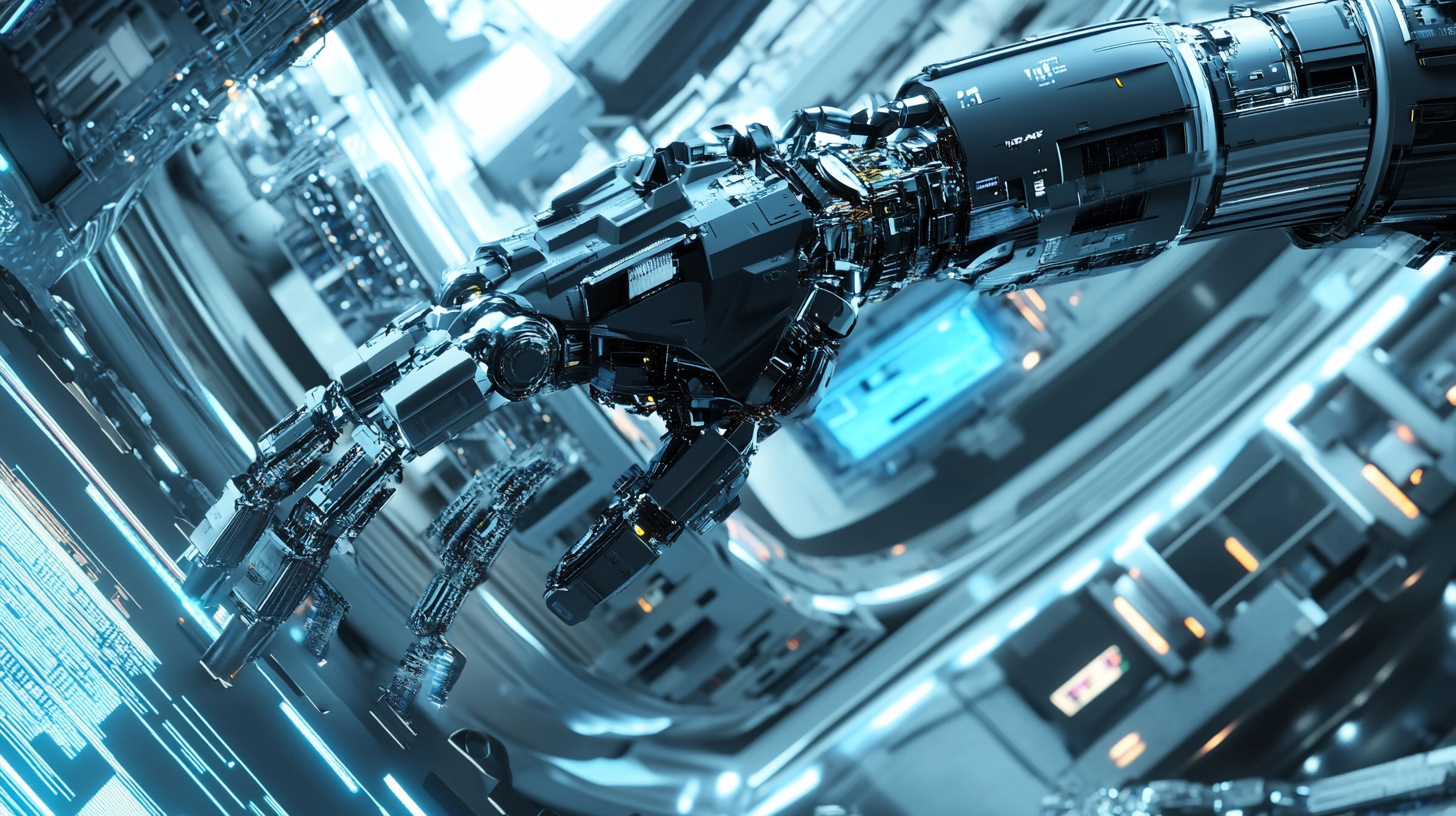
Sustainability in CNC Manufacturing: The Green Revolution
The evolution of CNC (Computer Numerical Control) manufacturing technologies is significantly contributing to a more sustainable future in global manufacturing. As industries begin to adopt newer methods, a key aspect gaining traction is subtractive manufacturing. This technique, which involves removing material to create parts, is revolutionizing how we perceive fabrication processes. By optimizing the use of raw materials and reducing waste, subtractive manufacturing is aligning with the global push towards sustainability.
Moreover, advancements in CNC technologies are enhancing efficiency while minimizing environmental impact. Modern CNC machines are designed to improve precision and reduce excess material use. This not only leads to less waste but also conserves energy, crucial factors in the quest for greener manufacturing practices. With features like automated tool changing and sophisticated software integration, manufacturers can achieve complex designs with minimal environmental footprint.
In addition, the focus on a circular economy is prompting manufacturers to rethink their supply chains and production methods. CNC technologies can facilitate the recycling of materials, allowing manufacturers to incorporate reclaimed resources into their processes. This shift not only supports sustainability but also drives innovation, leading to the development of new materials and processes that further reduce environmental impact. As we approach 2025, the integration of sustainability into CNC manufacturing is set to play a pivotal role in shaping the future of the industry.
Future Trends: Integrating AI and Automation with CNC Machines
As we approach 2025, the landscape of CNC machining is set to transform dramatically through the integration of AI and automation. Recent market analyses indicate that the global machine tool market is expected to experience substantial growth, with projections suggesting a significant uptick in demand due to advancements in operational technologies. From 2025 to 2034, capital investments in CNC machines are expected to flourish, driven not only by traditional sectors such as automotive and general machinery but also by emerging applications in precision mechanics and transport machinery.
The convergence of AI and CNC technology is advancing the capabilities of manufacturing processes, leading to smarter production lines. Reports indicate that the global market for AI and robotics could reach $44.3 billion by 2028, highlighting the increasing investment in intelligent automation solutions. Such technologies are revolutionizing the way manufacturers operate, with AI enabling predictive maintenance, adaptive control systems, and enhanced efficiency across production facilities. Factories equipped with cutting-edge CNC machinery are now capable of operating with minimal human intervention, optimizing productivity while reducing errors and operational costs.
In regions like Taiwan, which boast robust industrial supply chains, companies are uniquely positioned to leverage AI-driven innovations for competitive advantage. With the integration of 5G technology and advanced CNC machining techniques, manufacturers can expect to achieve significant efficiency gains, thereby reshaping industry standards and driving future growth. This technological synergy is paving the way for a new era in manufacturing, where adaptability and precision engineering are paramount to success.