5 Essential Insights for Sourcing Cnc Metal Milling Machines Globally
In the rapidly evolving world of manufacturing, the demand for precision and efficiency has placed CNC metal milling machines at the forefront of industrial production. These advanced machines are not only crucial for generating intricate parts and components but also play a significant role in enhancing operational workflows across various sectors. However, sourcing the right CNC metal milling machine globally can be a daunting task, given the plethora of options available in the market. Whether you are a seasoned manufacturer or a newcomer to the industry, understanding the intricacies of selecting the ideal machine is essential for achieving optimum results.
This blog will delve into five essential insights that can guide you through the global sourcing process of CNC metal milling machines. By examining key factors such as supplier reliability, technological advancements, cost considerations, and post-purchase support, you will be equipped with the knowledge necessary to make informed decisions. This comprehensive understanding will not only aid in procuring the best machines but also ensure that your investment leads to long-term success in your manufacturing endeavors.
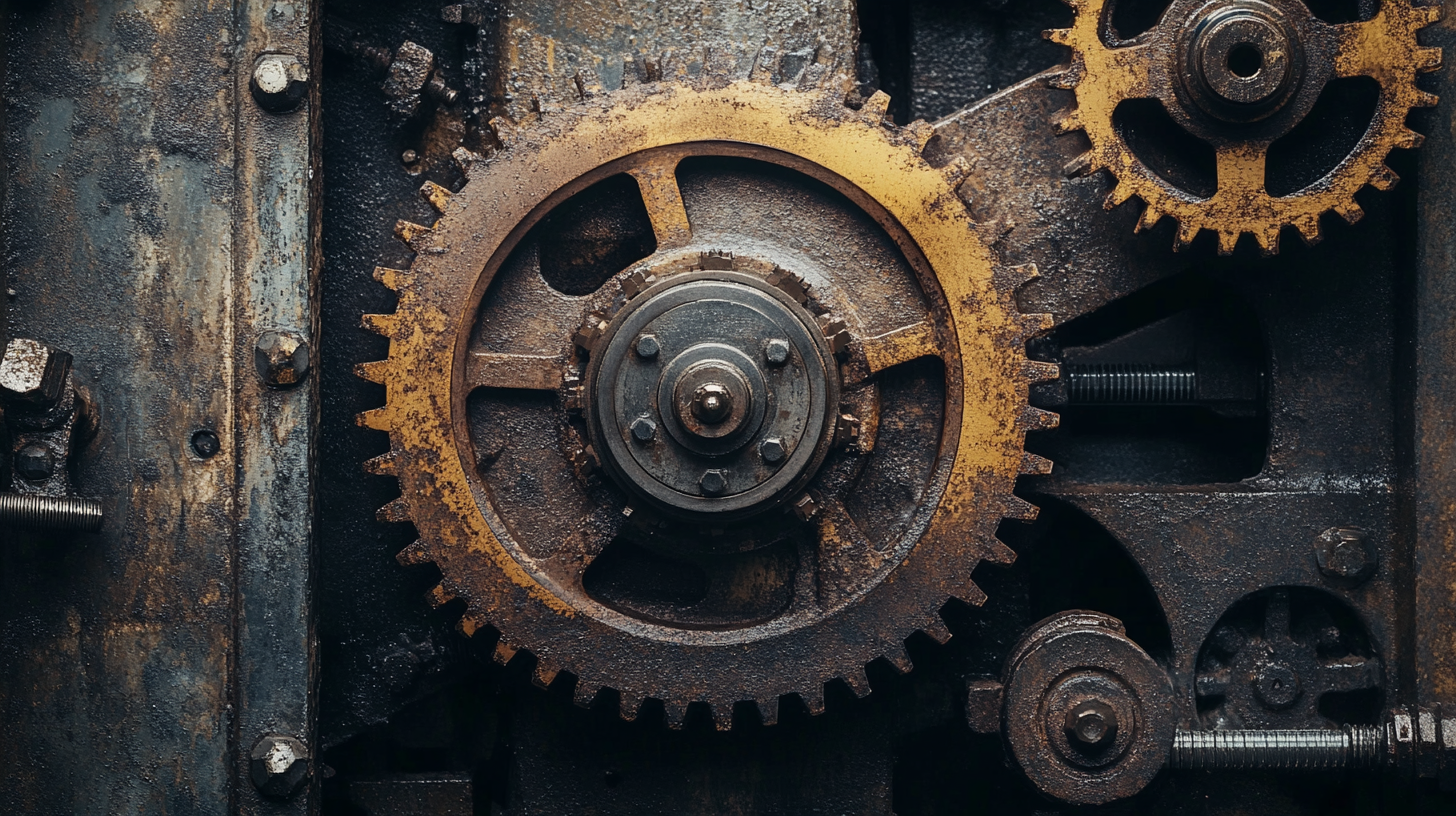
Key Considerations When Selecting CNC Metal Milling Machines
When selecting CNC metal milling machines for global sourcing, several key considerations must be taken into account. First, understanding the machine tool market size is essential. The growth trajectory of this market, fueled by industrial digitization and the increasing demand for precision engineering across various sectors, indicates a robust investment landscape. By analyzing industry stock trends and performance metrics, businesses can identify stable suppliers and potential partners that align with their strategic goals. The technology behind CNC milling machines plays a crucial role in the selection process. Conventional milling techniques are gradually being overshadowed by advanced CNC technologies, which offer enhanced precision, efficiency, and flexibility. Organizations must evaluate the specific applications they require—whether for automotive components, general machinery, or precision tools—since this will significantly influence their choice of machine. Additionally, examining the product categories, such as metal cutting and forming, is vital in ensuring that the selected machinery meets the operational needs of different industries. Regions that dominate the CNC market often offer varying levels of technological advancements and regulatory environments. It's imperative for enterprises to consider these regional dynamics and how they affect supply chain logistics, cost, and overall machine performance. By addressing these considerations, businesses can make informed decisions that optimize their manufacturing capabilities.
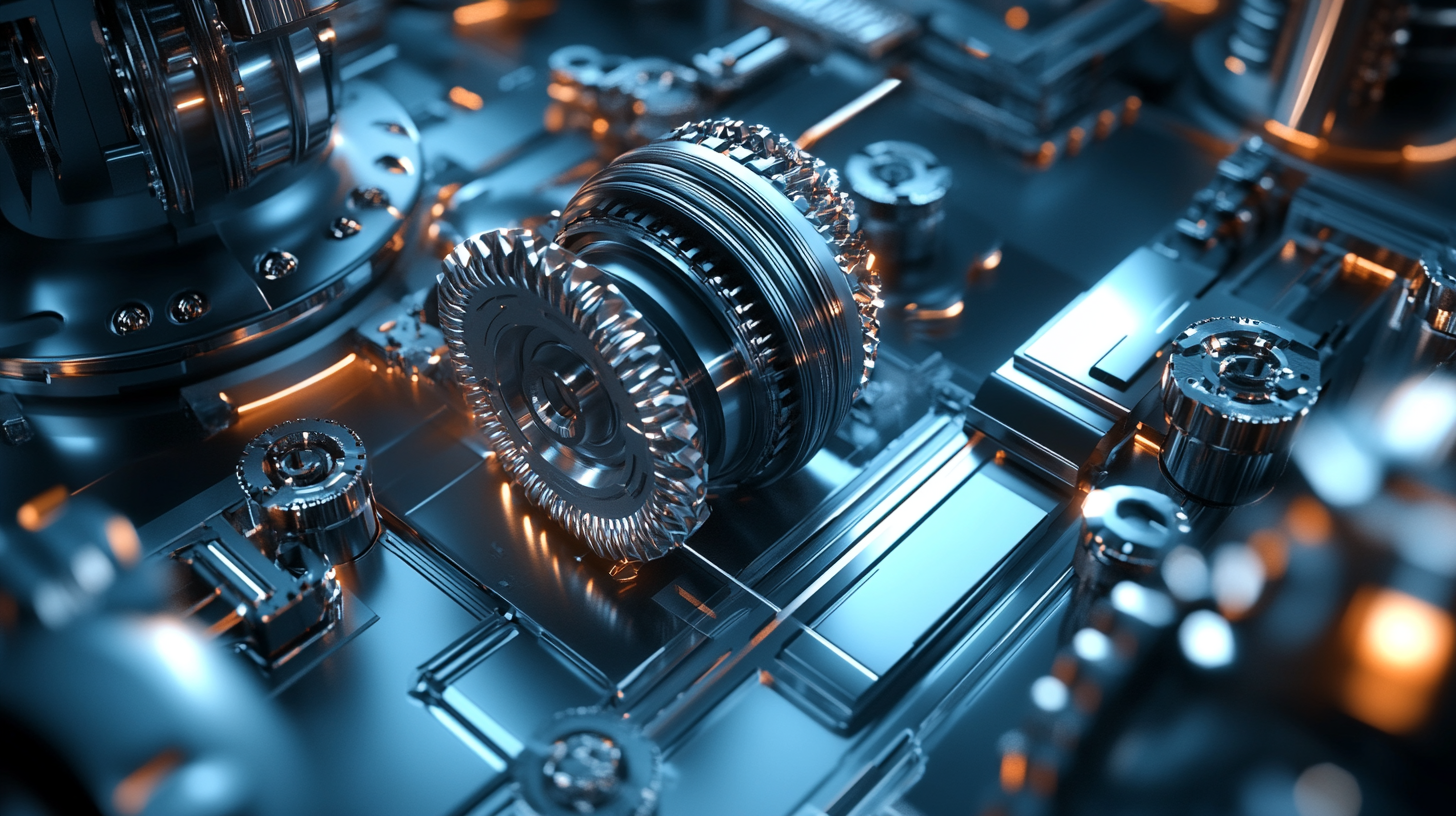
Understanding Global Sourcing: Benefits and Challenges
Global sourcing of CNC metal milling machines presents a unique set of benefits and challenges that businesses must navigate. One of the most significant advantages of sourcing these machines globally is the opportunity to access advanced technology and innovative features that may not be available domestically. Many manufacturers are located in regions that specialize in cutting-edge machining technologies, offering superior quality and performance. By sourcing from these countries, companies can enhance their production capabilities, achieve greater precision in machining, and stay competitive in a rapidly evolving market.
However, global sourcing does not come without its challenges. One of the primary concerns is managing the complexities of international logistics. Shipping machinery across borders can lead to delays, increased costs, and the potential for damage in transit. Additionally, businesses must navigate varying regulations and standards, which can complicate compliance and quality assurance processes. Establishing strong relationships with foreign suppliers is crucial, as effective communication and trust can mitigate risks associated with sourcing from different countries. Companies need to thoroughly vet suppliers and ensure they have robust quality control measures in place to prevent potential issues before they arise.
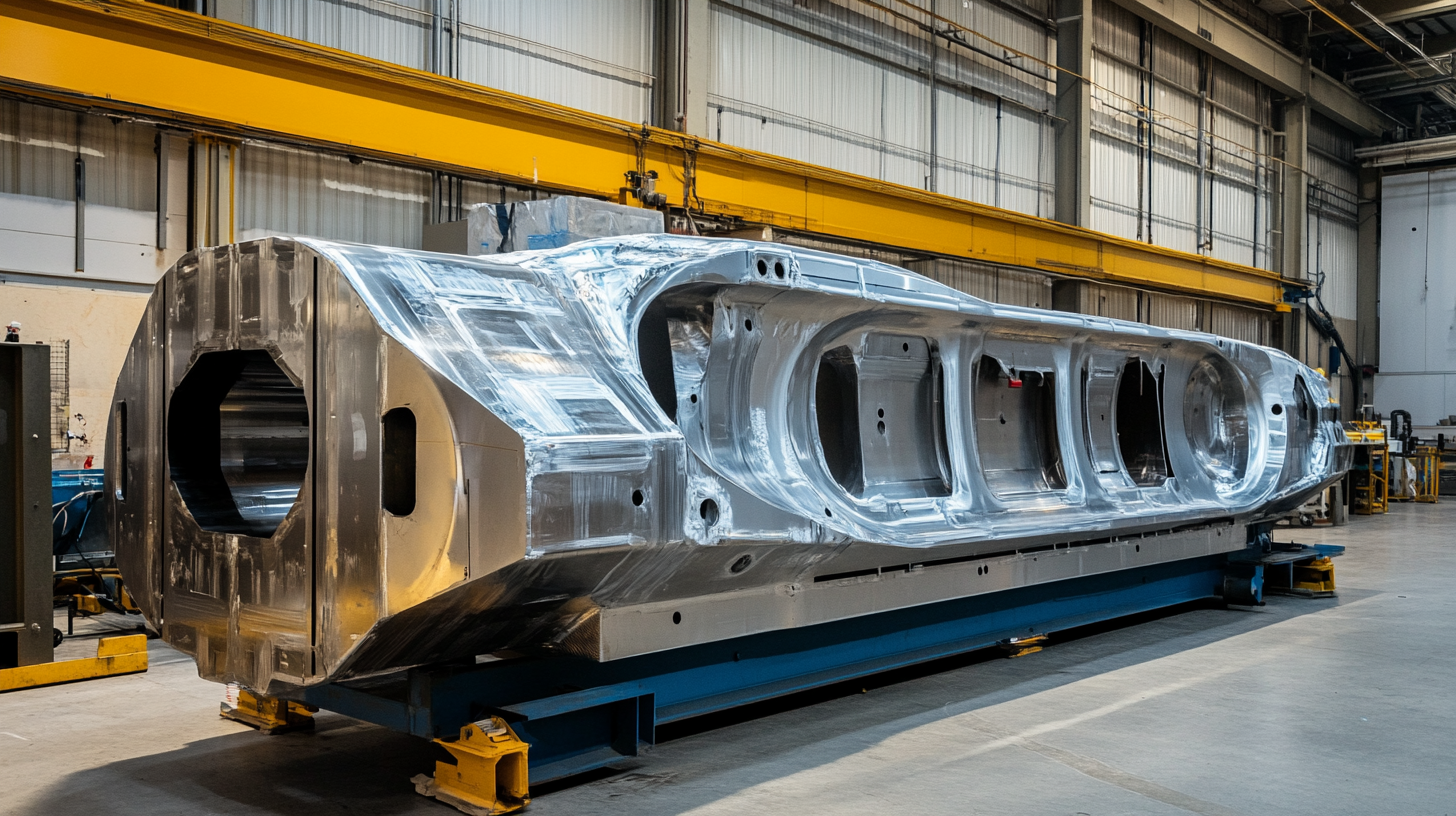
Evaluating Supplier Credentials and Manufacturing Capabilities
When sourcing CNC metal milling machines on a global scale, evaluating supplier credentials and manufacturing capabilities becomes paramount. First and foremost, a thorough assessment of the supplier’s history is essential. Reviewing their track record, including certifications, customer testimonials, and case studies, can provide insight into their reliability and reputation in the market. Quality management standards, such as ISO 9001, indicate that a supplier is committed to maintaining high quality in their manufacturing processes.
In addition to credentials, understanding the manufacturing capabilities of potential suppliers is crucial for ensuring that they can meet your specific needs. Factors such as the types of CNC machines they operate, their production capacity, and the skill level of their workforce directly impact the quality and efficiency of the milling processes. It is beneficial to conduct site visits where possible, allowing you to inspect their facilities, evaluate machinery, and assess the overall production environment. Engaging in direct communication with the suppliers about their technological advancements and workflow processes can further illuminate their ability to deliver high-performance CNC milling solutions tailored to your requirements.
Ultimately, a detailed evaluation of supplier credentials coupled with a comprehensive understanding of their manufacturing capabilities will empower businesses to make informed decisions in their global sourcing endeavors. This approach not only mitigates risks associated with subpar suppliers but also sets the foundation for long-term partnerships that drive innovation and efficiency in metalworking projects.
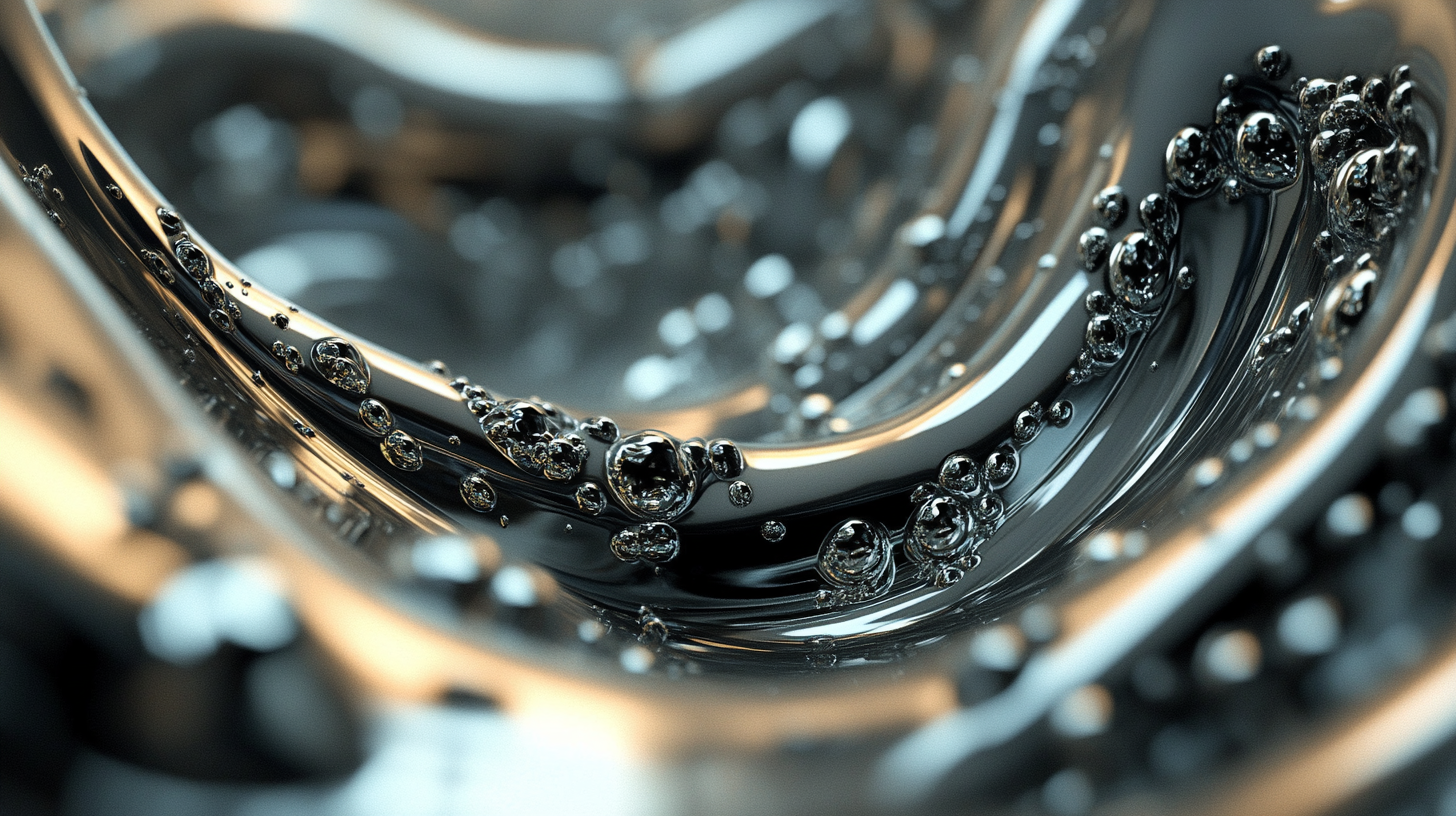
Cost Analysis: Balancing Quality and Price in CNC Machinery
In the global CNC metal milling machines market, striking the right balance between quality and price has become increasingly crucial for manufacturers and supply chain managers. According to recent industry reports, the CNC machine tool market is estimated to reach USD 100 billion by 2025, with a compound annual growth rate (CAGR) of approximately 6% during the forecast period. This growth is driven by the rising demand for precision engineering components across various sectors, including automotive, aerospace, and general machinery.
Cost analysis reveals that although high-quality CNC machines come with a premium price tag, investing in superior technology often results in long-term savings through reduced waste, lower maintenance costs, and enhanced productivity. For instance, advanced CNC systems equipped with automation features can lead to a reduction in labor costs by as much as 30%, making them an attractive option for businesses aiming to optimize their operations. However, firms must conduct thorough market research to assess prices across different regions, as costs can vary significantly based on local economic factors and supply chain efficiencies.
The market divides into categories based on products such as metal cutting and metal forming, and by application areas such as precision machinery and transport machinery. Each segment has distinct pricing dynamics influenced by technological advancements and material costs. Furthermore, geographies like North America, Europe, and the Asia-Pacific are witnessing varying growth trends, with the Asia-Pacific region projected to dominate market share, driven by increased manufacturing activities and investments in modern tooling technology.
Trends in CNC Technology: What to Look for in Modern Machines
The global CNC machine tool market is poised for significant growth, with projections indicating an increase from USD 120.19 billion in 2024 to approximately USD 230.42 billion by 2033, representing a compound annual growth rate (CAGR) of 7.50% during the forecast period from 2025 to 2033. This upward trend is influenced by the rising demand for high-precision manufacturing across various industries, including automotive, general machinery, and aerospace. As companies strive to enhance operational efficiency, the integration of CNC technology is increasingly becoming a focal point in their strategies.
As we look into trends in CNC technology, it is essential to identify key features in modern machines. The shift towards digital transformation in the manufacturing sector has accelerated the adoption of advanced CNC tools that offer enhanced flexibility and automation capabilities. Notably, the market for indexable milling cutters is also on the rise, with various analyses highlighting factors such as blade material, coating type, and the number of cutting edges as determinants of market share and growth projections between 2024 and 2032.
Moreover, the CNC machine tool market is witnessing technological innovations that cater to specific applications. For instance, the automotive and precision machinery sectors are increasingly opting for machines that support complex geometries and high-speed operations. This trend reflects an overarching commitment to adopting smart technologies that not only improve product quality but also optimize production processes to meet the evolving demands of end-users in a competitive landscape.