Setting the Benchmark: Global Standards and Innovations in Metal Milling Machine Production
In the rapidly evolving landscape of manufacturing, the significance of Metal Milling Machines cannot be overstated. As defined by recent industry reports, the global metalworking machinery market, which includes milling machines, is projected to reach an estimated USD 93.7 billion by 2026, growing at a CAGR of 5.2% from 2021 to 2026. This growth is expected to be driven by advancements in technology and the increasing demand for precision components across various sectors such as aerospace, automotive, and electronics. The shift towards automation and smart manufacturing solutions further underlines the necessity for state-of-the-art metal milling machines that not only improve efficiency but also enhance product quality.
Moreover, innovations such as computer numerical control (CNC) technology are revolutionizing metal milling processes, allowing manufacturers to achieve high levels of precision and repeatability. Reports suggest that the adoption of CNC milling machines is anticipated to contribute significantly to this market growth, as companies seek to reduce production costs and lead times while meeting stringent quality standards. As we explore the benchmarks set by industry leaders in metal milling machine production, it becomes essential to examine how these innovations are reshaping manufacturing practices and setting new standards on a global scale.
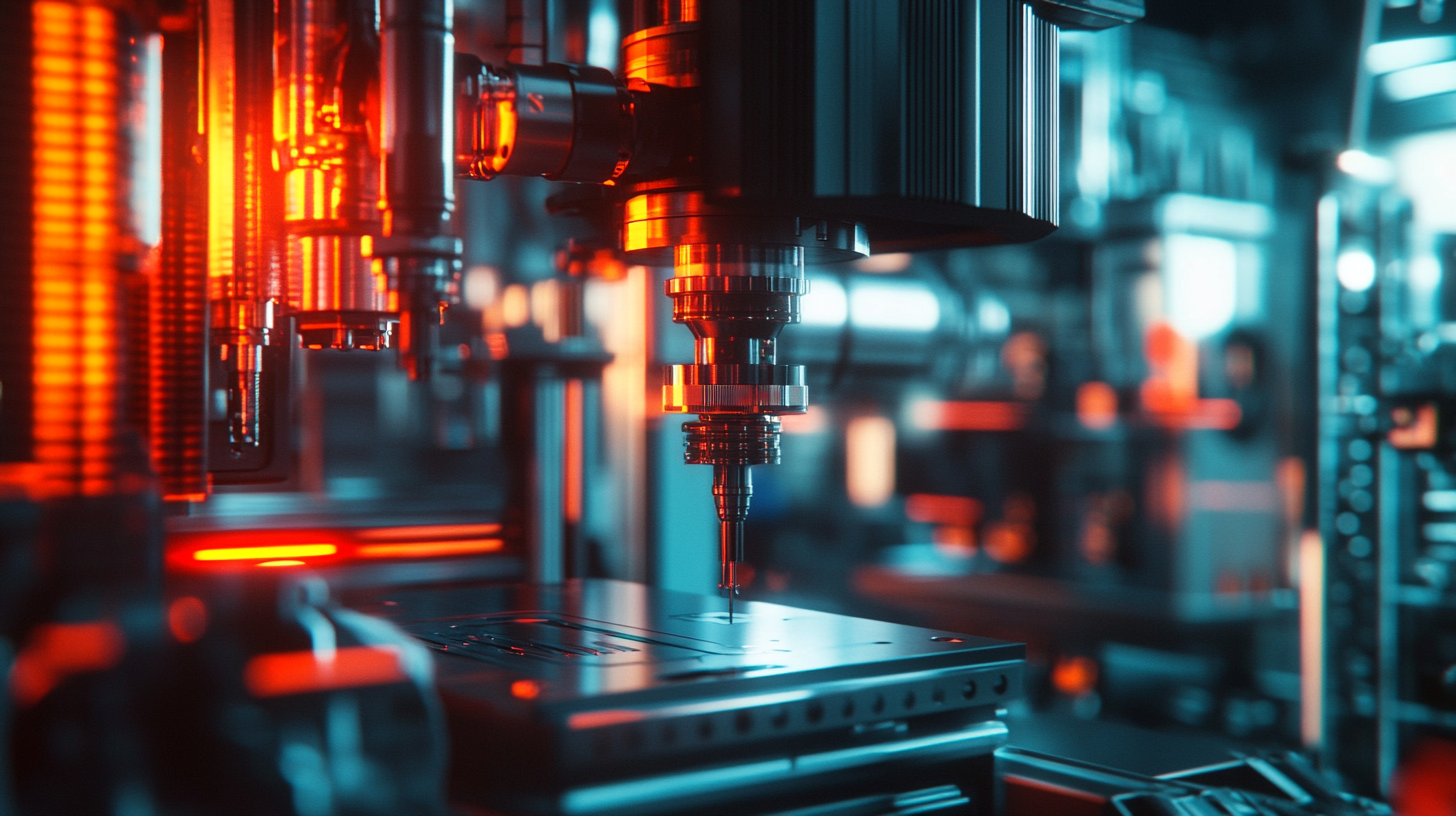
Global Standards in Metal Milling Machine Production: An Overview
The global metal milling machine production sector is undergoing significant transformations, driven by innovations and adherence to global standards. According to the "World Steel in Figures 2023," the dynamics of the steel industry are evolving, reflecting a strong demand for high-quality steel products essential for machine tooling. This increased demand underscores the need for precision in manufacturing processes, particularly in metal milling, which relies heavily on the integrity and quality of the raw materials used. Recent reports indicate that the metal machining market is poised for robust growth, with projections estimating an increase of USD 18.43 billion from 2024 to 2028. This surge is largely propelled by rising requirements from industries such as oil and gas, where advanced machining capabilities are vital. Additionally, with the global CNC machine market anticipated to expand significantly, expected to rise from $101.22 billion in 2025 to $195.59 billion by 2032, the metal milling machine sector is well-positioned to leverage these developments. Technological advancements play a crucial role in this evolution. For instance, the integration of artificial intelligence is revolutionizing traditional machining processes, enhancing efficiency and precision. Manufacturers are increasingly adopting automation and digital solutions to meet stringent global standards, ensuring competitiveness in international markets. As nations strive toward sustainability, low-carbon production methods are becoming imperative, paving the way for innovations that align with environmental goals while maintaining the quality required in metal milling applications.
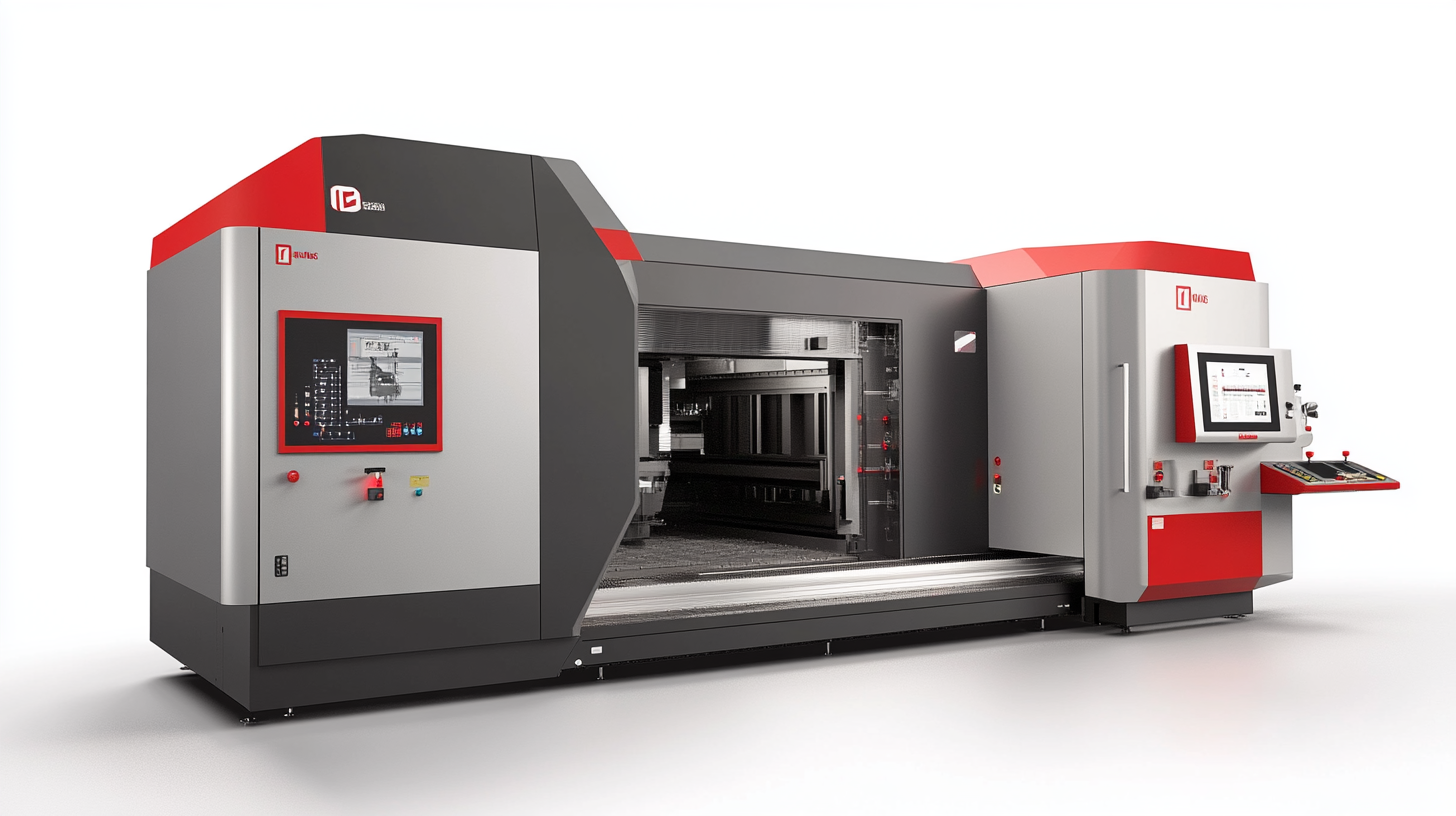
Innovative Technologies Revolutionizing Metal Milling Machines
Innovative technologies are set to revolutionize the metal milling machine production landscape, driving efficiency and performance to unprecedented levels. According to a recent market research report by Grand View Research, the global metal cutting machine tools market is anticipated to reach $114.6 billion by 2026, growing at a CAGR of 6.3% from 2019 to 2026. This growth can largely be attributed to advancements in automation, artificial intelligence (AI), and precision engineering that are reshaping how manufacturers approach milling operations.
One of the most significant innovations is the integration of AI-driven predictive maintenance in milling machines. This technology allows for real-time monitoring of machine performance, predicting potential failures before they occur, thereby minimizing downtime and reducing operational costs. A report by McKinsey & Company highlighted that companies implementing predictive maintenance strategies can expect a reduction in maintenance costs by up to 30% and a 10% increase in productivity.
Another trend is the adoption of additive manufacturing techniques alongside traditional milling processes. By incorporating additive elements, manufacturers can create more complex geometries and optimize the use of materials. According to a study by Deloitte, nearly 90% of manufacturers are investing in additive technologies, recognizing their potential to transform conventional workflows and enhance product functionality.
Furthermore, the introduction of smarter, more user-friendly interfaces in CNC machines is making it easier for operators to program and utilize milling machines effectively. These advancements are not only improving accuracy and efficiency but also enabling a more seamless integration of technology in smaller workshops where skilled labor may be limited. As the industry continues to embrace these innovations, we can expect metal milling machines to become more accessible and capable, setting a new benchmark for manufacturing standards.
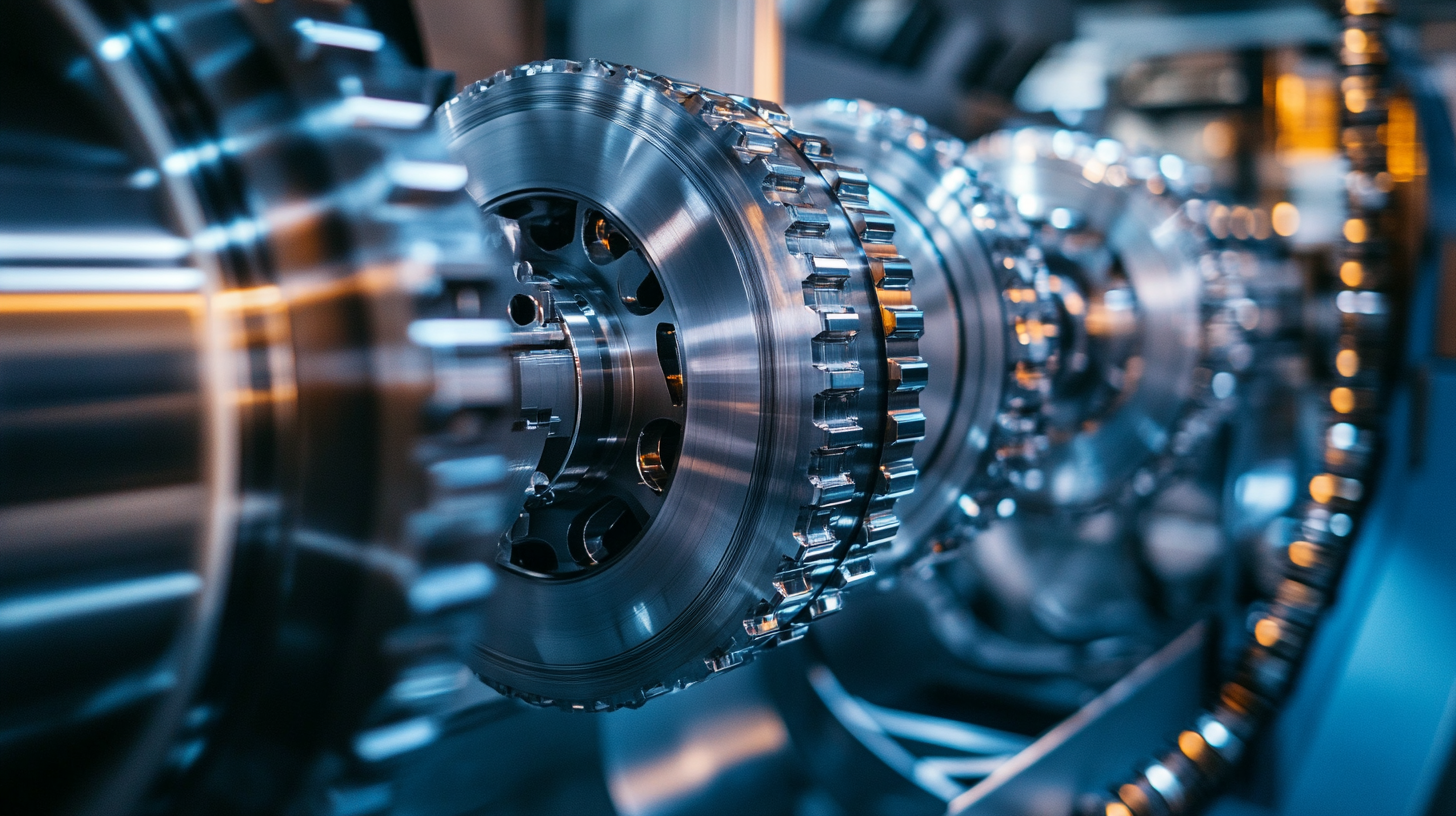
Sustainability Initiatives in Metal Milling Machine Manufacturing
In the modern manufacturing landscape, sustainability initiatives have become a cornerstone of success in the production of metal milling machines. As industry leaders recognize the environmental impacts of traditional manufacturing processes, they are actively implementing innovative solutions to reduce waste and enhance efficiency. This shift not only addresses ecological concerns but also meets the increasing demand from consumers and regulatory bodies for greener practices.
One significant initiative within the metal milling machine sector is the adoption of renewable energy sources during production. By integrating solar panels and wind turbines into their operations, manufacturers can drastically cut down on their carbon footprint. Additionally, many companies are exploring partnerships with energy providers to source sustainable electricity, thereby ensuring that the entire manufacturing process aligns with eco-friendly principles.
Another critical aspect of sustainability is the development of advanced materials and technologies that enhance the efficiency of milling machines. Manufacturers are investing in research to create lighter, more durable materials that require less energy during production and operation. Furthermore, innovations such as closed-loop water recycling systems are being implemented to minimize water consumption, demonstrating a commitment to conserving resources.
Through these sustainability initiatives, the metal milling machine industry is setting a benchmark for environmentally responsible manufacturing. As businesses evolve to embrace these practices, they not only contribute to a more sustainable future but also position themselves as leaders in an increasingly eco-conscious market.
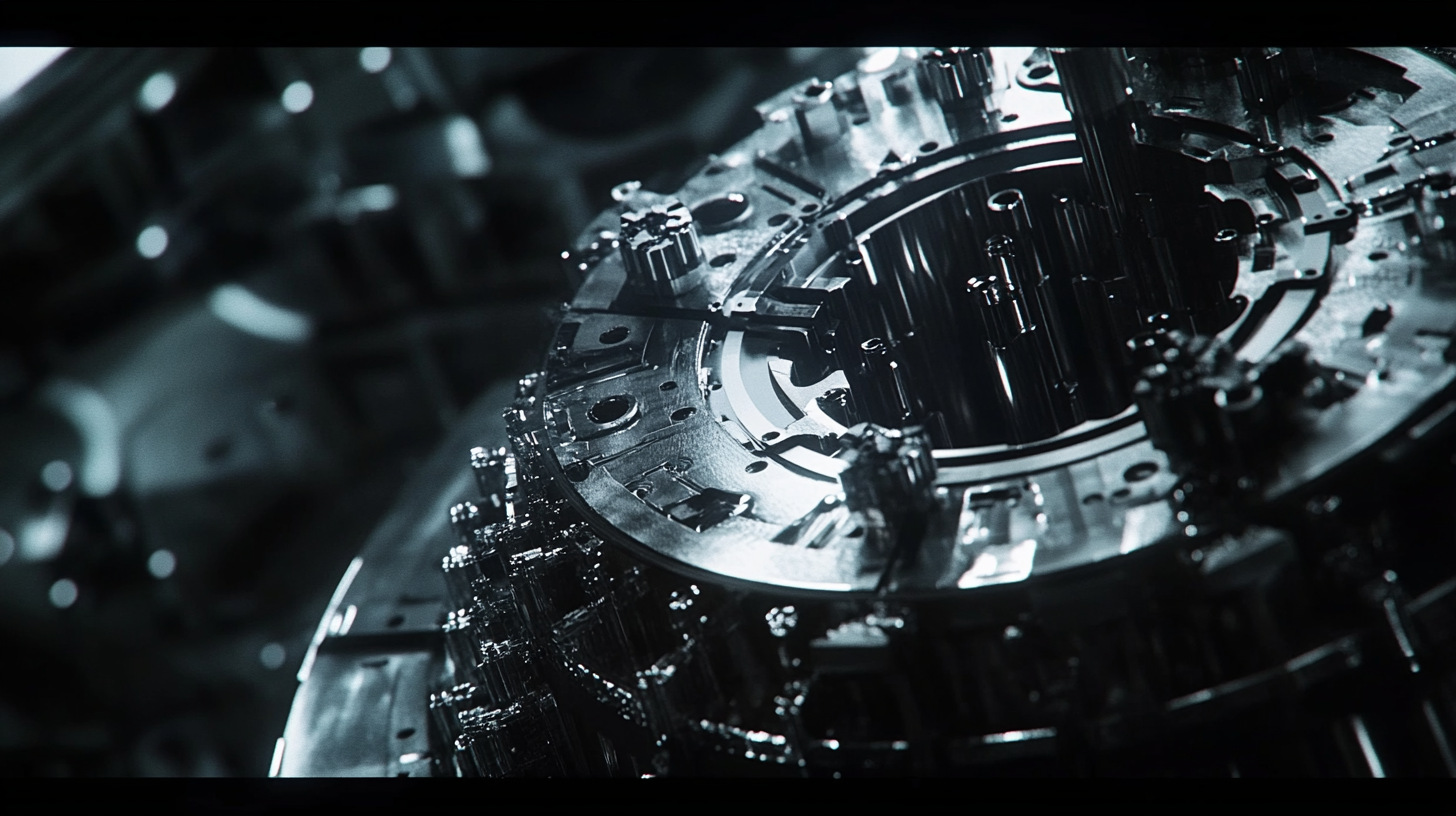
Comparative Analysis of Global Metal Milling Machine Standards
In the competitive landscape of metal milling machine production, global standards play a pivotal role in setting benchmarks that manufacturers must adhere to. These standards not only ensure quality and safety but also foster technological innovation across different regions. A comparative analysis reveals that while countries like Germany and Japan lead the way with their stringent quality control protocols, emerging markets such as China and India are rapidly adopting similar standards to enhance their manufacturing capabilities.
One notable aspect of these global standards is the emphasis on precision and efficiency. For instance, the ISO 9001 certification has become a baseline metric for machine tools, promoting a uniform approach to quality management. Companies adhering to these standards often invest in advanced technologies, such as CNC (computer numerical control) machining, to optimize their production processes. This investment in technology not only improves product reliability but also positions manufacturers favorably in international markets.
Moreover, the push for sustainability is reshaping the standards within the metal milling machine industry. Countries are increasingly adopting guidelines that not only focus on the performance of machines but also consider environmental impact. Innovations like energy-efficient motors and eco-friendly materials are becoming crucial criteria in the comparative analysis of global standards. As manufacturers strive to meet these evolving benchmarks, the industry is not just witnessing a technological transformation but also a profound shift toward sustainable practices that will define the future of metal milling production.
Future Trends in Metal Milling Machine Innovations and Standards
In the ever-evolving field of manufacturing, metal milling machines have undergone remarkable transformations driven by technological advancements and global standards. As industries increasingly prioritize precision and efficiency, innovations such as automation, artificial intelligence, and advanced materials are setting new benchmarks for production capabilities. The future of metal milling machines lies in their ability to integrate these technologies to enhance productivity, reduce waste, and increase flexibility in manufacturing processes.
One of the significant trends shaping the future of metal milling machine production is the integration of smart technologies. The rise of the Internet of Things (IoT) allows machines to communicate in real-time, facilitating predictive maintenance and improved operational efficiency. Moreover, the incorporation of advanced software solutions for simulation and programming is enabling manufacturers to streamline workflows and optimize production schedules. As these technologies continue to mature, they are expected to redefine the boundaries of traditional machining practices.
Additionally, sustainability is becoming a critical focus in the development of metal milling machines. There is a growing demand for machines designed to minimize energy consumption and reduce environmental impact. Innovations such as energy-efficient motors and recyclable materials are gaining traction, aligning with global standards for sustainable manufacturing. As industries navigate these changes, the implementation of robust environmental practices will be essential to meet regulatory requirements and consumer expectations.