Exploring Innovative Alternatives to Small Milling Machines: A Data-Driven Approach for Enhanced Precision
In the ever-evolving landscape of manufacturing, the significance of precision engineering cannot be overstated. Small milling machines have long been a staple in workshops and factories, facilitating intricate machining processes with efficiency. According to the latest report from Research and Markets, the small milling machine market is projected to reach a significant value of $1.8 billion by 2026, driven by rising demand for compact and versatile solutions across various industries. However, as technology advances, the limitations of traditional small milling machines become increasingly apparent, including challenges in precision, speed, and adaptability. This blog explores innovative alternatives to small milling machines, leveraging a data-driven approach to enhance precision and meet the growing demands of modern manufacturing. By examining emerging technologies and methodologies, we aim to highlight how the industry can transition towards more effective and accurate machining solutions, ensuring sustained competitiveness in a rapidly changing marketplace.
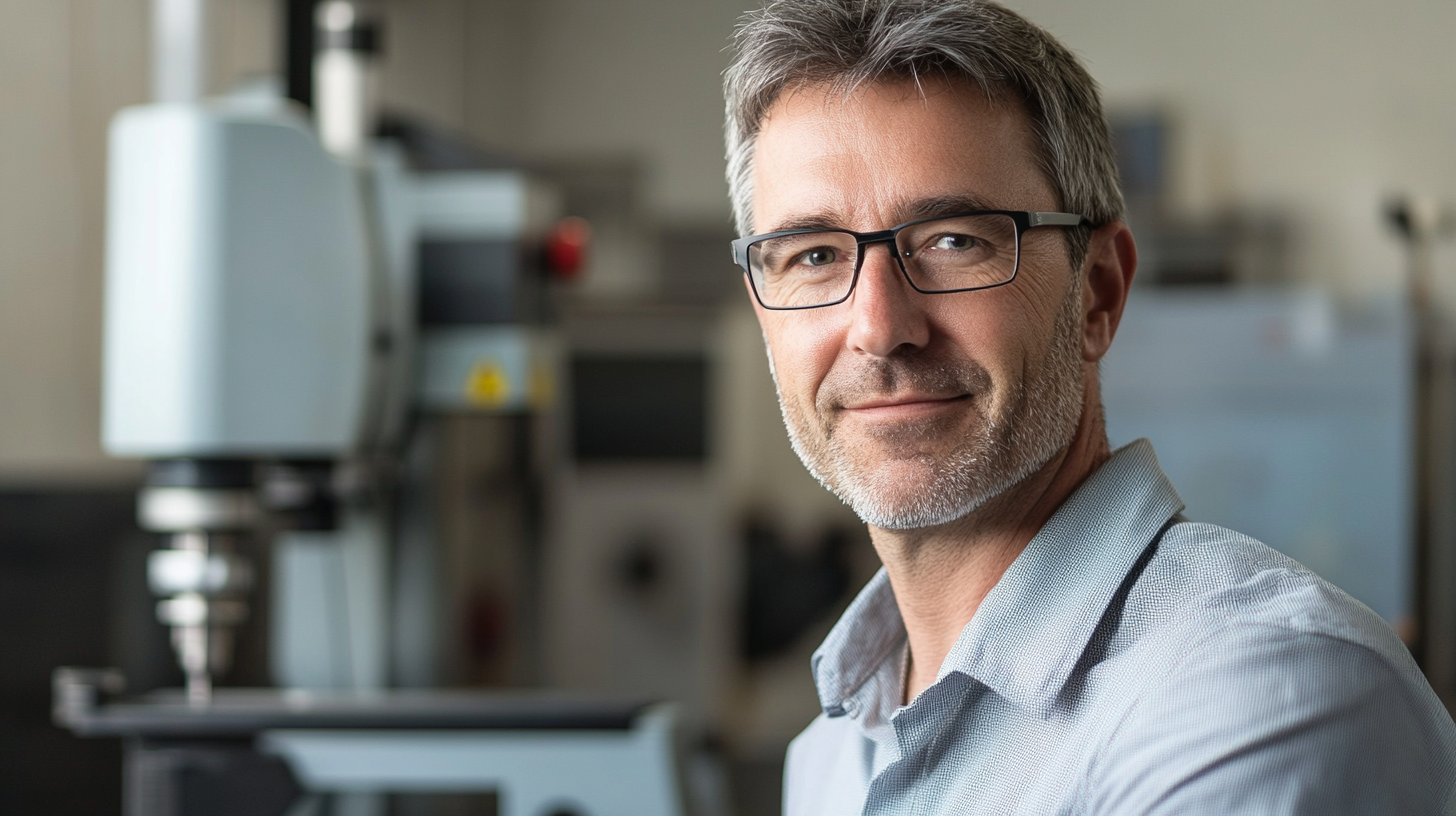
Examining Current Trends in Small Milling Machine Precision and Performance Metrics
In the realm of small milling machines, precision and performance metrics stand as crucial factors influencing their effectiveness in various applications. Recent advancements in machine learning techniques have opened new avenues for enhancing the precision of milling processes. By examining the microstructure of materials through innovative data-driven approaches, researchers are unveiling the relationships between material characteristics and performance outcomes. This analysis not only aids in predicting material properties but also enhances the reverse engineering process, ultimately contributing to improved milling precision.
Moreover, the exploration of cutting parameters in laser cutting has also shed light on how surface quality and kerf dimensions can be optimized. By leveraging comprehensive reviews and data analysis, manufacturers can now refine their operational parameters to achieve better outcomes in milling and cutting operations. This intersection of technology and manufacturing practices reflects a shift towards more intelligent and efficient machining solutions, ensuring that small milling machines meet the evolving demands of precision engineering. The ongoing studies in material behavior under various machining conditions present a roadmap for the future of milling technologies, highlighting the significance of integrating data analytics in optimizing performance metrics.
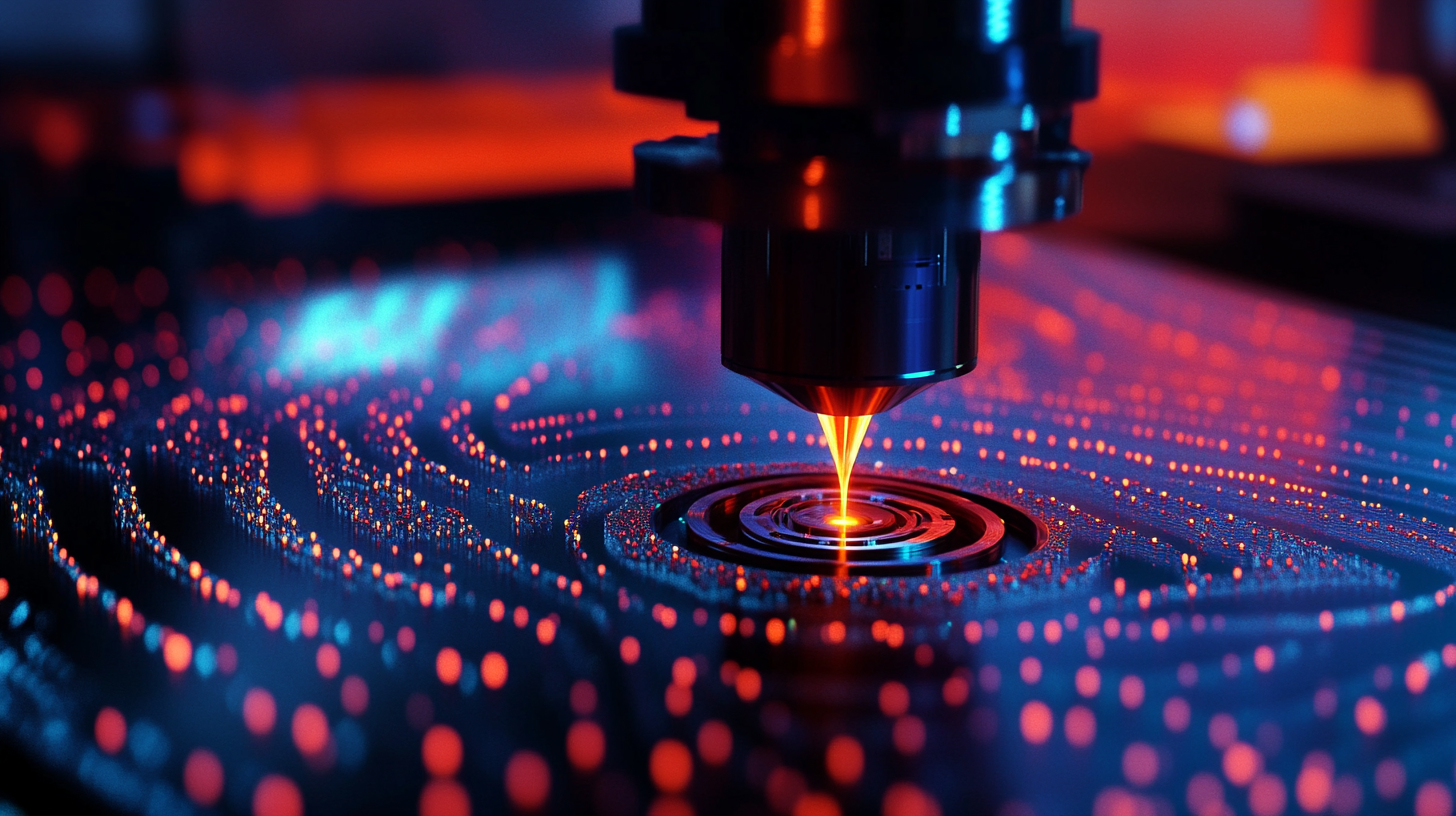
Analyzing the Limitations of Traditional Small Milling Machines in Precision Engineering
Small milling machines have long been a staple in precision engineering, yet their limitations have increasingly come into focus. According to a report by Grand View Research, the global precision engineering market is projected to reach $964 billion by 2025, indicating a significant shift towards more advanced technologies. One key shortcoming of traditional small milling machines is their inability to maintain consistent accuracy over extended periods, largely due to mechanical wear and vibration. A study conducted by the University of Cambridge found that such machines can deviate by as much as 0.1 mm after only a few hours of operation, which can lead to significant losses in material and time.
Moreover, the integration of advanced materials and complex geometries in modern manufacturing further exacerbates the issues associated with traditional milling techniques. A report from the American Society of Mechanical Engineers highlights that up to 30% of machining costs can be attributed to inefficiencies caused by conventional milling processes. This has prompted engineers to explore innovative alternatives like additive manufacturing and hybrid machining techniques, which promise not only improved precision but also enhanced flexibility for intricate designs. Such approaches could potentially revolutionize the industry, offering a more sustainable and cost-effective solution to the challenges posed by traditional small milling machines.
Evaluating Emerging Technologies for Enhanced Milling Accuracy and Efficiency
In the realm of precision milling, emerging technologies are transforming the landscape. Recent studies emphasize the importance of key performance indicators (KPIs) in evaluating production efficiency, particularly in the food industry. By adopting a holistic approach to performance measurement, businesses can significantly enhance their milling processes. For instance, leveraging metrics such as machine downtime, processing speeds, and output quality allows manufacturers to identify bottlenecks and streamline operations, ultimately leading to higher milling accuracy and reduced waste.
Furthermore, the integration of artificial intelligence and machine learning in Industry 4.0 is revolutionizing production process optimization. These technologies provide real-time analytics and predictive maintenance capabilities that are crucial for small milling machines. Reports indicate that AI-driven systems can improve precision by up to 30% through adaptive control mechanisms. Workshops focusing on standards for absolute accuracy, particularly in robotic applications, are key for sharing knowledge and fostering innovation. This exchange of ideas is essential for advancing techniques that ensure both efficiency and unparalleled accuracy in milling operations.
Exploring Innovative Alternatives to Small Milling Machines
This pie chart illustrates the percentage of different innovative technologies that enhance milling accuracy and efficiency. Each segment represents a technology's contribution to improved precision in milling operations.
Case Studies: Successful Implementation of Innovative Milling Alternatives in Industry
In the manufacturing sector, particularly in precision engineering, the adoption of innovative milling alternatives has been gaining traction. Several industries are transitioning from traditional small milling machines to advanced technologies, leveraging data analytics and automation to enhance productivity and precision. The case studies of companies that have successfully implemented these alternatives reveal that investing in innovative milling technologies leads to improved output quality and reduced operational costs. For instance, a leading automotive manufacturer implemented a sophisticated CNC system, resulting in a 30% increase in production speed without sacrificing precision.
Moreover, as industries adapt to the digital transformation trends highlighted in the financial and fintech sectors, they are also incorporating smart solutions into their milling processes. The integration of Internet of Things (IoT) devices enables real-time monitoring and predictive maintenance, reducing downtime and enhancing performance. One notable case is a medical device manufacturer that utilized data-driven insights to optimize their milling processes, achieving tighter tolerances and significantly lowering material waste. This shift not only underscores the importance of innovation in manufacturing but also highlights how data-centric approaches can transform traditional practices, leading to greater efficiency and sustainability in the industry.
Case Study | Industry | Innovative Alternative | Precision Improvement (%) | Cost Reduction (%) |
---|---|---|---|---|
Case Study A | Aerospace | Laser Milling | 25 | 20 |
Case Study B | Automotive | 3D Printed Tools | 30 | 15 |
Case Study C | Medical Devices | High-Speed Machining | 40 | 18 |
Case Study D | Electronics | Ultrasonic Milling | 35 | 22 |
Future Prospects: Predictive Data Analytics in Small Milling Solutions for Optimal Outcomes
In the evolving landscape of small milling machines, predictive data analytics offers unprecedented opportunities for enhanced precision and efficiency. By harnessing vast datasets, businesses can perform comprehensive cost-benefit analyses that weigh the projected expenses against the anticipated outcomes of milling operations. This approach not only aids in making informed decisions but also enhances the overall operational effectiveness by minimizing waste and maximizing the output quality.
As industries increasingly turn to digitalization to meet sustainable development goals, the integration of predictive analytics in milling solutions stands out. This shift enables the creation of interconnected networks that capitalize on previously untapped big data. The result is a robust framework that allows for real-time adjustments and optimizations in milling processes, enhancing precision and reducing costs. By leveraging advanced technologies, businesses can anticipate potential issues, streamline production, and achieve optimal outcomes in their milling operations.
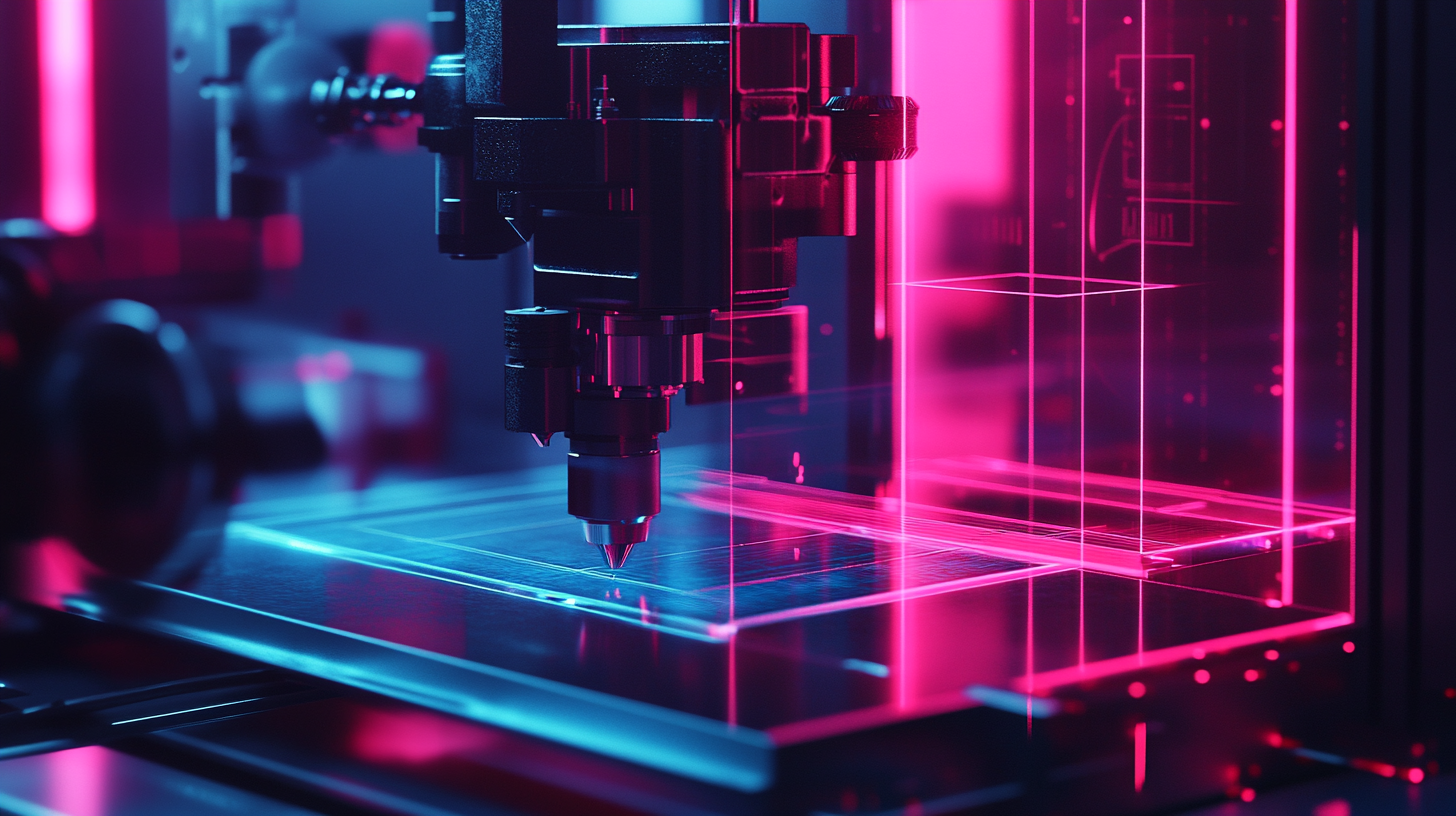